Preparation method of sponge-structured iron/sic particle-based oil-water separation enhancement layer material
A technology of oil-water separation and structural type, which is applied in the preparation field of sponge-structured iron/SiC particle-based oil-water separation enhancement layer materials, can solve the problems of environmental secondary pollution, achieve strong adsorption, strong drainage, and oil-water separation efficiency high effect
- Summary
- Abstract
- Description
- Claims
- Application Information
AI Technical Summary
Problems solved by technology
Method used
Image
Examples
Embodiment 1
[0032] The preferred embodiment 1 of the present invention provides a method for preparing a sponge structure iron / SiC nanoparticle composite material, which includes the following steps in sequence:
[0033] ① Conductive treatment of polyurethane sponge model: mix nano carbon powder, nano iron powder, ethyl hydroxyethyl cellulose, xanthan gum, sodium silicate and deionized water to form a conductive slurry. The mass percentages of the components in the conductive slurry are: 18% nano-carbon powder, 20% nano-iron powder, 3% ethyl hydroxyethyl cellulose, 5% xanthan gum, 1.5% ammonium bicarbonate, and the rest are Deionized water: After fully soaking the polyurethane sponge in the conductive slurry, the conductive polyurethane sponge model is obtained after 4 hours of drying in a 35°C drying box.
[0034] ②Sponge structure iron / SiC nanoparticle matrix composite electrodeposition treatment: the concentration is analytically pure iron oxide, 37% by mass hydrochloric acid, sodium lactat...
Embodiment 2
[0038] The preferred embodiment 2 of the present invention provides a method for preparing a sponge-structured iron / SiC nanoparticle composite material with reduced surface energy, which includes the following steps in sequence:
[0039] ① Conductive treatment of polyurethane sponge model: mix nano carbon powder, nano iron powder, ethyl hydroxyethyl cellulose, xanthan gum, sodium silicate and deionized water to form a conductive slurry. The mass percentages of the components in the conductive slurry are: 18% nano-carbon powder, 20% nano-iron powder, 3% ethyl hydroxyethyl cellulose, 5% xanthan gum, 1.5% ammonium bicarbonate, and the rest are Deionized water: After fully soaking the polyurethane sponge in the conductive slurry, the conductive polyurethane sponge model is obtained after 4 hours of drying in a 35°C drying box.
[0040] ②Sponge structure iron / SiC nanoparticle matrix composite electrodeposition treatment: the concentration is analytically pure iron oxide, 37% by mass hyd...
Embodiment 3
[0045] The preferred embodiment 3 of the present invention provides a method for preparing a sponge structure iron / SiC nanoparticle-based superhydrophobic / super lipophilic enhanced layer oil-water separation material, which includes the following steps in sequence:
[0046] ① Conductive treatment of polyurethane sponge model: mix nano carbon powder, nano iron powder, ethyl hydroxyethyl cellulose, xanthan gum, sodium silicate and deionized water to form a conductive slurry. The mass percentages of the components in the conductive slurry are: 18% nano-carbon powder, 20% nano-iron powder, 3% ethyl hydroxyethyl cellulose, 5% xanthan gum, 1.5% ammonium bicarbonate, and the rest are Deionized water: After fully soaking the polyurethane sponge in the conductive slurry, the conductive polyurethane sponge model is obtained after 4 hours of drying in a 35°C drying box.
[0047] ②Sponge structure iron / SiC nanoparticle matrix composite electrodeposition treatment: the concentration is analytic...
PUM
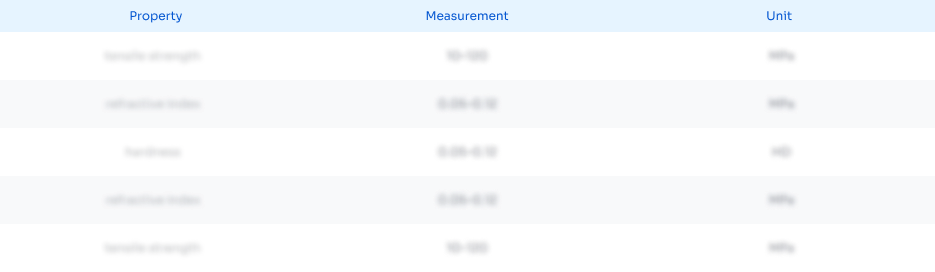
Abstract
Description
Claims
Application Information

- R&D Engineer
- R&D Manager
- IP Professional
- Industry Leading Data Capabilities
- Powerful AI technology
- Patent DNA Extraction
Browse by: Latest US Patents, China's latest patents, Technical Efficacy Thesaurus, Application Domain, Technology Topic, Popular Technical Reports.
© 2024 PatSnap. All rights reserved.Legal|Privacy policy|Modern Slavery Act Transparency Statement|Sitemap|About US| Contact US: help@patsnap.com