Water-borne wax-emulsion shoe polish finishing agent based on anionic polyurethane modified oxidized wax and preparation method of water-borne wax-emulsion shoe polish finishing agent
A technology of polyurethane modification and wax oxidation, which is applied in the direction of chemical instruments and methods, polishing compositions, etc. It can solve the problems of leather fading, strong irritating taste, resistance to wet friction, poor durability and water resistance, etc., and achieve good adhesion and interface Strong effect, non-flammable effect
- Summary
- Abstract
- Description
- Claims
- Application Information
AI Technical Summary
Problems solved by technology
Method used
Image
Examples
Embodiment 1
[0030] 1. Preparation of polyurethane modified oxidized wax emulsion:
[0031] 100g of oxidized paraffin, 6g of propylene glycol butyl ether (solvent), 2g of Vulkanox BHT (stabilizer), and 9g of polytetrahydrofuran ether glycol (Mn=2000) were heated up until the oxidized wax was completely melted, and stirred at a speed of 250r / min for 8min; 14g of IPDI (isophorone diisocyanate) and 6g of DMBA (dimethylol butyric acid) were reacted at a temperature of 110°C for 110min to prepare a polyurethane-modified oxidized wax containing a hydrophilic group, and the temperature was lowered to 65°C to add 18g of methyl Silicone oil: increase the speed to 850r / min, add 45g of deionized water with 9g of triethylamine dropwise within 25min, keep stirring and shearing at 1400r / min for 20min, then add 62g of deionized water in three times to obtain polyurethane modified Oxidized wax emulsion.
[0032] 2. Formulation of water-based wax shoe polish finishing agent
[0033]
[0034]
[003...
Embodiment 2
[0038] 1. Preparation of polyurethane modified oxidized wax emulsion:
[0039] After 70g of oxidized paraffin wax and 30g of polyethylene oxide wax, 8g of diethylene glycol butyl ether (solvent), 2g of Tinuvin 213 (stabilizer), and 8g of polycaprolactone glycol (Mn=2000) are heated up to the complete melting of the oxidized wax , stirred at a speed of 300r / min for 7min; added 13g of IPDI (isophorone diisocyanate) and 6g of DMBA (dimethylol butyric acid), and reacted at a temperature of 110°C for 100min to obtain a hydrophilic group-containing polyurethane modified To oxidize the wax, cool down to 70°C and add 16g of methyl silicone oil; increase the speed to 950r / min, add 50g of deionized water with 8g of triethylamine dropwise within 25 minutes, keep stirring and shearing at 1300r / min for 25 minutes, and then divide it into three times Add 65g of deionized water to obtain polyurethane modified oxidized wax emulsion.
[0040] 2. Formulation of water-based wax shoe polish fini...
Embodiment 3
[0045] 1. Preparation of polyurethane modified oxidized wax emulsion:
[0046] 40g of oxidized paraffin wax, 60g of polyethylene oxide wax, 9g of N,N-dimethylformamide (solvent), 3g of Tinuvin 327 (stabilizer), and 7g of polycarbonate diol (Mn=1000) were heated until the oxidized wax was completely After melting, stir at a speed of 350r / min for 6min; add 11g of HDI (hexamethyl diisocyanate) and 6g of DMPA (dimethylolpropionic acid), and react at a temperature of 105°C for 95min to obtain a polyurethane containing a hydrophilic group To modify the oxidized wax, cool down to 75°C and add 16g of methyl silicone oil; increase the speed to 900r / min, add 55g of deionized water with 6.5g of triethylamine dropwise within 25min, keep stirring and shearing for 25min at 1250r / min, Then, 68 g of deionized water was added three times to obtain a polyurethane-modified oxidized wax emulsion.
[0047] 2. Formulation of water-based wax shoe polish finishing agent
[0048]
[0049] 3. Prep...
PUM
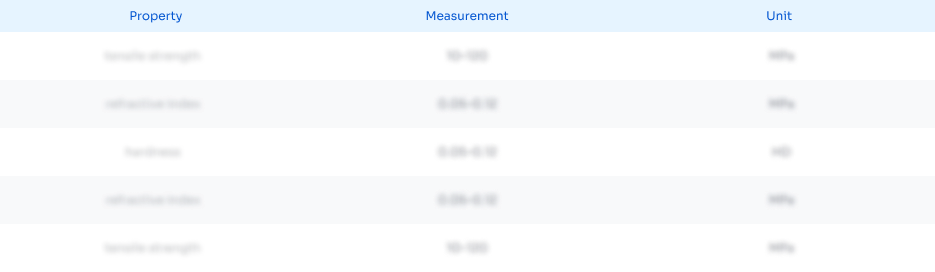
Abstract
Description
Claims
Application Information

- R&D
- Intellectual Property
- Life Sciences
- Materials
- Tech Scout
- Unparalleled Data Quality
- Higher Quality Content
- 60% Fewer Hallucinations
Browse by: Latest US Patents, China's latest patents, Technical Efficacy Thesaurus, Application Domain, Technology Topic, Popular Technical Reports.
© 2025 PatSnap. All rights reserved.Legal|Privacy policy|Modern Slavery Act Transparency Statement|Sitemap|About US| Contact US: help@patsnap.com