Nylon composite material
A nylon composite material and nylon technology, which is applied in the field of nylon composite materials, can solve the problems such as inability to balance performance, and achieve the effects of improving poor toughness, little influence on material color, and reducing the amount of addition
- Summary
- Abstract
- Description
- Claims
- Application Information
AI Technical Summary
Problems solved by technology
Method used
Image
Examples
preparation example Construction
[0024] For example, the present invention provides a preparation method of modified inorganic fillers: add inorganic fillers and water into a flask, stir evenly, add emulsifier OP-10 [nonylphenol polydec(ethylene oxide) alcohol], high-speed After stirring for 30 minutes, add 25% monomer (methyl acrylate), emulsify at high speed for 30 minutes, heat up to 60-70°C, add 50% of initiator, that is, 50% of the total amount of initiator, and heat up to 80-90°C ℃, add the remaining monomers and initiators synchronously, keep the temperature at 80-90 ℃, evenly add in 3 hours, keep warm for 1 hour, cool to room temperature, filter, refrigerate, demulsify, wash, and vacuum dry to obtain modification Inorganic filler. For example, the outermost monomer methacrylic acid (MAA) is 0.5% of the total mass of the shell monomer methyl acrylate (MMA). In another example, the initiator is potassium sulfate.
[0025] Specifically in this embodiment, the grafted elastomer is maleic anhydride graft...
Embodiment 1
[0044] Nylon composite material in the embodiment of the present invention 1 comprises the following components in the following weight percentages:
[0045] Nylon 6: 81.1%, grafted elastomer: 16%, modified inorganic filler: 2%, lubricant: 0.3%, antioxidant: 0.6%.
[0046] The preparation method of nylon composite material in the embodiment of the present invention 1, comprises the following steps:
[0047] Nylon 6 was dried at 100°C for 6 hours. The dried nylon 6, modified inorganic filler, grafted elastomer, lubricant, and antioxidant were stirred in a high-speed mixer for 3 minutes and then added to the hopper of the twin-screw extruder. The process conditions of the twin-screw extruder were set as: 1 The temperature in the zone is 200-220°C, the temperature in the second zone is 220-240°C, the temperature in the third zone is 220-240°C, the temperature in the fourth zone is 220-250°C, the temperature in the fifth zone is 220-250°C, and the temperature in the sixth zone is...
Embodiment 2
[0049] Nylon composite material in the embodiment of the present invention 2 comprises the following components in the following weight percentages:
[0050] Nylon 6: 79.1%, grafted elastomer: 18%, modified inorganic filler: 2%, lubricant: 0.3%, antioxidant: 0.6%.
[0051] The preparation method of the nylon composite material in Example 2 of the present invention is the same as that in Example 1.
PUM
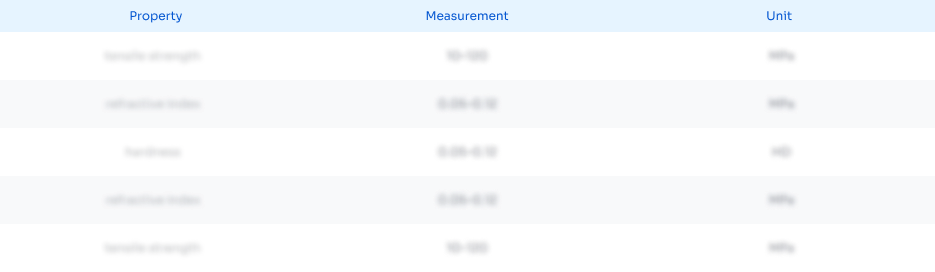
Abstract
Description
Claims
Application Information

- Generate Ideas
- Intellectual Property
- Life Sciences
- Materials
- Tech Scout
- Unparalleled Data Quality
- Higher Quality Content
- 60% Fewer Hallucinations
Browse by: Latest US Patents, China's latest patents, Technical Efficacy Thesaurus, Application Domain, Technology Topic, Popular Technical Reports.
© 2025 PatSnap. All rights reserved.Legal|Privacy policy|Modern Slavery Act Transparency Statement|Sitemap|About US| Contact US: help@patsnap.com