Preparation method of quartz ceramic product with complex structure
A technology of quartz ceramics and complex structure, which is applied in the field of preparation of complex structure quartz ceramic products, can solve the problems of complex shape and internal structure of quartz ceramic products, and achieve the effect of good appearance, enhanced fluidity and less internal defects
- Summary
- Abstract
- Description
- Claims
- Application Information
AI Technical Summary
Problems solved by technology
Method used
Examples
Embodiment 1
[0024] Step 1: Powder Mixing
[0025] The purity of the selected high-purity fused silica powder raw material is greater than 99.99wt%.
[0026] Mix the selected fused silica powder, wherein the particle size distribution and mass fraction of the fused silica powder are: 5-8μm, 4wt%; 8-21μm, 8wt%; 21-58μm, 20wt%; 58-114μm , 39wt%; 114-160μm, 19wt%; 160-175μm, 10wt%; add the above-mentioned high-purity fused silica powder to 0.4% lactic acid and 0.15% trisodium bicarbonate, and stir evenly to obtain a mixed Powder.
[0027] Step 2: Prepare the Slurry
[0028] Mix 75wt% polyethylene wax, 18wt% vaseline, 5wt% beeswax, and 2wt% rosin to make a binder, heat and melt in a water bath at 90°C, and then pour the mixed powder in step 1 into the binder, Stir evenly to obtain a slurry, wherein the mass of the binder is 16% of the mass of the quartz powder in step 1.
[0029] The polyethylene wax used in the adhesive has a molecular weight of 1500-1650. The molecular weight of polyethy...
Embodiment 2
[0034] In this embodiment, the process conditions and raw materials are consistent with those in Example 1, the difference is that in step 1, the high-purity fused silica powder is also added with Si that accounts for 0.6% by mass. 3 N 4 Powder. The particle size of the powder is 30 μm.
Embodiment 3
[0036] In this embodiment, the process conditions and raw materials are consistent with those in Example 1, the difference is that in step 1, the high-purity fused silica powder is also added with 1% Al 2 o 3 Powder. The particle size of the powder is 30 μm.
PUM
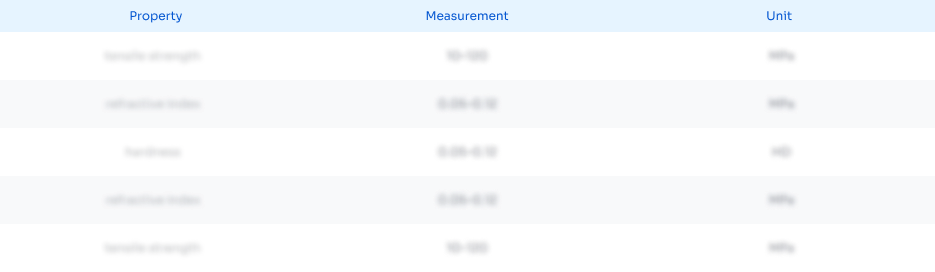
Abstract
Description
Claims
Application Information

- Generate Ideas
- Intellectual Property
- Life Sciences
- Materials
- Tech Scout
- Unparalleled Data Quality
- Higher Quality Content
- 60% Fewer Hallucinations
Browse by: Latest US Patents, China's latest patents, Technical Efficacy Thesaurus, Application Domain, Technology Topic, Popular Technical Reports.
© 2025 PatSnap. All rights reserved.Legal|Privacy policy|Modern Slavery Act Transparency Statement|Sitemap|About US| Contact US: help@patsnap.com