Method for preparing frits for ceramic glazes from high temperature liquid industrial slag
A ceramic glaze and high temperature technology is applied in the field of producing frit for ceramic glaze, can solve the problem of not involving the use of high temperature liquid industrial slag high temperature energy, etc., and achieves the effects of suitable expansion coefficient, wide firing temperature and high strength
- Summary
- Abstract
- Description
- Claims
- Application Information
AI Technical Summary
Problems solved by technology
Method used
Image
Examples
Embodiment 1
[0038]According to parts by weight, 5 parts of fly ash, 45 parts of quartz sand, 20 parts of sodium carbonate, 5 parts of sodium nitrate and 1 part of antimony trioxide are uniformly mixed in advance to prepare a solid conditioning material for use.
[0039] Discharge the high-temperature liquid Corex direct smelting reduction ironmaking slag of 80 parts by weight into the glass melting furnace, add the above-mentioned prepared tempering material at the same time, and heat at 1450 °C for 6 hours in the melting furnace to melt the tempering material and Mix evenly with slag to obtain a clarified and homogenized melt.
[0040] The melt is discharged from the melting kiln, and the melt is flushed with cold water at the same time, so that the melt is quenched into frit particles, and the frit particles are dried, broken, and sieved to obtain frit products for ceramic transparent glazes. The coefficient of thermal expansion (0~600℃) is (6.4~6.6)xl0 -6 / °C, the Mohs hardness of the...
Embodiment 2
[0043] According to the parts by weight in advance, 5 parts of zircon sand, 20 parts of quartz sand, 20 parts of feldspar, 8 parts of magnesia and 10 parts of borax are uniformly mixed to prepare a solid conditioning material for use.
[0044] Put 50 parts by weight of high-temperature liquid yellow phosphorus slag into the electric arc furnace, add the above-mentioned prepared tempering material at the same time, heat in the electric arc furnace for 1 hour, and melt the tempering material.
[0045] Pour the melt into the tank kiln and heat it at 1430°C for 4 hours in the tank kiln to obtain a clarified and homogenized melt.
[0046] The melt is discharged from the tank kiln, and the melt is flushed with cold water to quench the melt into frit particles, and the frit particles are dried, broken and sieved to obtain frit products for ceramic microcrystalline glazes. Block thermal expansion coefficient (0~600℃) is (6.5~6.7)xl0 -6 / °C, the Mohs hardness on the surface of the gla...
PUM
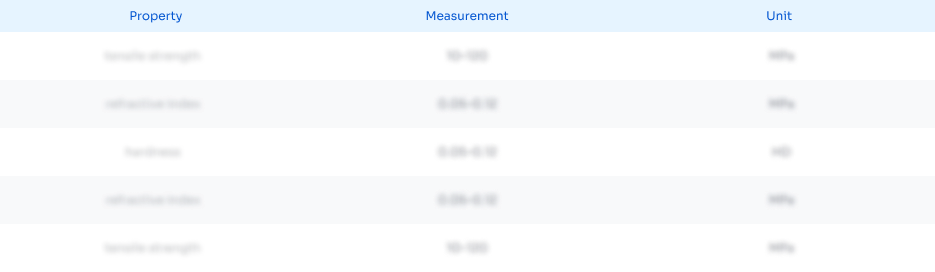
Abstract
Description
Claims
Application Information

- Generate Ideas
- Intellectual Property
- Life Sciences
- Materials
- Tech Scout
- Unparalleled Data Quality
- Higher Quality Content
- 60% Fewer Hallucinations
Browse by: Latest US Patents, China's latest patents, Technical Efficacy Thesaurus, Application Domain, Technology Topic, Popular Technical Reports.
© 2025 PatSnap. All rights reserved.Legal|Privacy policy|Modern Slavery Act Transparency Statement|Sitemap|About US| Contact US: help@patsnap.com