A preparation method for in-situ growth of three-dimensional graphene on the surface of spherical copper powder
An in-situ growth and graphene technology, applied in metal processing equipment, gaseous chemical plating, coating, etc., can solve the problems of graphene damage, orientation restriction, graphene agglomeration, etc., and achieve the effect of strengthening
- Summary
- Abstract
- Description
- Claims
- Application Information
AI Technical Summary
Problems solved by technology
Method used
Image
Examples
Embodiment 1
[0037] Put polymethyl methacrylate and steel balls into a ball mill jar with a mass ratio of 1:15, and fill it with argon as a protective atmosphere. Go through low-speed short-time ball milling (400 rpm, ball milling 2h) in a planetary ball mill. Scanned photographs of spherical polymethyl methacrylate as Figure 1a As shown, the photo of polymethyl methacrylate after ball milling is shown in Figure 1b As shown, the surface of PMMA after ball milling is relatively rough, which is suitable for the adhesion of copper powder.
Embodiment 2
[0039] Put polymethyl methacrylate and steel balls into a ball mill jar with a mass ratio of 1:20, and fill it with argon as a protective atmosphere. Go through low-speed short-time ball milling (400 rpm, ball milling 2h) in a planetary ball mill. Scanned photographs of spherical polymethyl methacrylate as figure 2 As shown, at this time, due to the increase of the ball-to-material ratio, PMMA sticks and overlaps due to long-term impact during the deformation process, resulting in poor dispersion of PMMA, which is not conducive to subsequent mixing with copper powder. Example 3
Embodiment 3
[0040]Put polymethyl methacrylate and steel balls into a ball mill jar with a mass ratio of 1:10, and fill it with argon as a protective atmosphere. Go through low-speed short-time ball milling (400 rpm, ball milling 2h) in a planetary ball mill. Scanned photographs of spherical polymethyl methacrylate as image 3 As shown, the deformation and roughness of PMMA did not reach the ideal level at this time due to the decrease of the ball-to-material ratio.
PUM
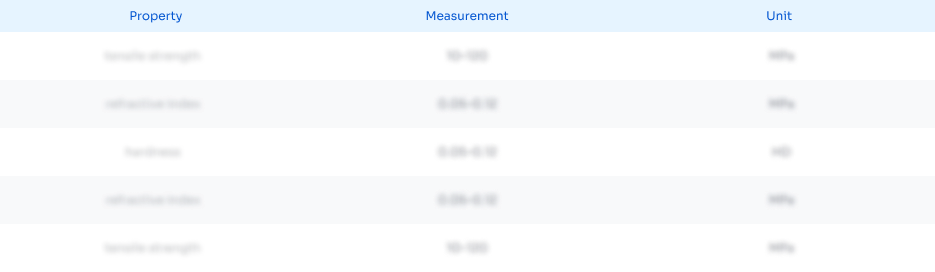
Abstract
Description
Claims
Application Information

- R&D
- Intellectual Property
- Life Sciences
- Materials
- Tech Scout
- Unparalleled Data Quality
- Higher Quality Content
- 60% Fewer Hallucinations
Browse by: Latest US Patents, China's latest patents, Technical Efficacy Thesaurus, Application Domain, Technology Topic, Popular Technical Reports.
© 2025 PatSnap. All rights reserved.Legal|Privacy policy|Modern Slavery Act Transparency Statement|Sitemap|About US| Contact US: help@patsnap.com