Flue gas denitration catalyst and preparation method thereof
A denitrification catalyst and flue gas technology, applied in chemical instruments and methods, physical/chemical process catalysts, separation methods, etc., can solve problems such as catalyst wear, boiler matching difficulties, shorten catalyst service life, etc., and achieve good load and good catalysis Function, the effect of strong anti-sulfur poisoning performance
- Summary
- Abstract
- Description
- Claims
- Application Information
AI Technical Summary
Problems solved by technology
Method used
Image
Examples
Embodiment 1
[0027] A flue gas denitrification catalyst, which uses glass fiber powder as a carrier, manganese acetate and potassium perchlorate (mass ratio: 1:0.5) are loaded as active components, and ferric oxide and cerium oxide (mass ratio: 1:1.5) are used as active ingredients. Co-catalyst; wherein, the mass ratio of active ingredient, co-catalyst and carrier is 1:5:58.
[0028] The preparation method of above-mentioned a kind of flue gas denitrification catalyst comprises steps:
[0029] (1) take ferric oxide, cerium oxide of formula quantity, mix uniformly, obtain mixed powder;
[0030] (2) manganese acetate and potassium perchlorate of formula quantity are dissolved in deionized water, obtain aqueous solution;
[0031] (3) mixing the mixed powder obtained in step (1) with the aqueous solution obtained in step (2), and stirring evenly to obtain a mixed slurry;
[0032] (4) Add activated glass fiber powder to the mixed slurry, stir for 12 hours, dry at 80° C. for 5 hours, and calci...
Embodiment 2
[0034] A flue gas denitrification catalyst, which uses glass fiber powder as a carrier, manganese acetate and potassium perchlorate (mass ratio: 1:2) as active components, and ferric oxide and cerium oxide (mass ratio: 1:3) as active components. Co-catalyst; wherein, the mass ratio of active ingredient, co-catalyst and carrier is 1:12:75.
[0035] The preparation method of above-mentioned a kind of flue gas denitrification catalyst comprises steps:
[0036] (1) take ferric oxide, cerium oxide of formula quantity, mix uniformly, obtain mixed powder;
[0037] (2) manganese acetate and potassium perchlorate of formula quantity are dissolved in deionized water, obtain aqueous solution;
[0038] (3) mixing the mixed powder obtained in step (1) with the aqueous solution obtained in step (2), and stirring evenly to obtain a mixed slurry;
[0039] (4) Add activated glass fiber powder to the mixed slurry, stir for 15 hours, dry at 130°C for 8 hours, and calcined at 430°C for 45 hours...
Embodiment 3
[0041] A flue gas denitrification catalyst, which uses glass fiber powder as a carrier, manganese acetate and potassium perchlorate (mass ratio: 1:0.5) are loaded as active components, and ferric oxide and cerium oxide (mass ratio: 1:1.5) are used as active ingredients. The co-catalyst, in addition, also includes hydroxypropyl methylcellulose; wherein, the mass ratio of active ingredient, co-catalyst, carrier and hydroxypropyl methyl cellulose is 1:5:58:2.
[0042] The preparation method of above-mentioned a kind of flue gas denitrification catalyst comprises steps:
[0043] (1) take ferric oxide, cerium oxide and hydroxypropyl methylcellulose of formula quantity, mix uniformly, obtain mixed powder;
[0044] (2) manganese acetate and potassium perchlorate of formula quantity are dissolved in deionized water, obtain aqueous solution;
[0045] (3) mixing the mixed powder obtained in step (1) with the aqueous solution obtained in step (2), and stirring evenly to obtain a mixed s...
PUM
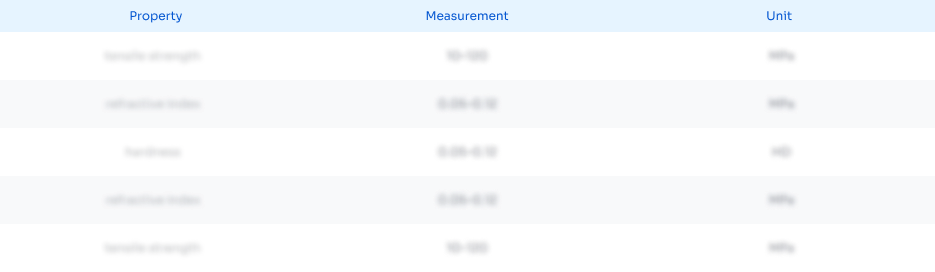
Abstract
Description
Claims
Application Information

- R&D Engineer
- R&D Manager
- IP Professional
- Industry Leading Data Capabilities
- Powerful AI technology
- Patent DNA Extraction
Browse by: Latest US Patents, China's latest patents, Technical Efficacy Thesaurus, Application Domain, Technology Topic, Popular Technical Reports.
© 2024 PatSnap. All rights reserved.Legal|Privacy policy|Modern Slavery Act Transparency Statement|Sitemap|About US| Contact US: help@patsnap.com