Inorganic hydrated salt phase change energy storage microcapsule and preparation method thereof
A technology of inorganic hydrated salt and phase change energy storage, which is applied in the field of preparation of energy storage microcapsule materials, and achieves the effects of simple process, reduced supercooling degree and low cost
- Summary
- Abstract
- Description
- Claims
- Application Information
AI Technical Summary
Problems solved by technology
Method used
Image
Examples
preparation example Construction
[0022] In order to realize the preparation of the above-mentioned inorganic phase change energy storage microcapsules, the specific steps are as follows:
[0023] (1) adding the core material to deionized water to prepare a saturated solution of the core material;
[0024] (2) Add the emulsifier to the saturated solution of the core material. The quality of the emulsifier is 0.001 to 0.2 times the mass of the core material. Ultrasonic emulsify in an ultrasonic cell pulverizer or ultrasonic cleaning machine for 20 to 50 minutes, and then in 35 to Using magnetic stirring in a water bath at 60°C for 30 to 60 minutes at a speed of 600 to 1200 rpm to obtain a uniformly dispersed core material emulsion (A);
[0025] (3) Add the wall material prepolymer into the organic phase, and continue stirring for 30 minutes at a speed of 600-1000 rpm in a magnetic stirrer to obtain a transparent prepolymer solution (B); the wall material prepolymer The amount of polymer added is based on the c...
Embodiment 1
[0033] (1) Weigh 15g of sodium thiosulfate pentahydrate, dissolve it in 20mL of deionized water to form a solution, add 0.6-1.0g of sodium lauryl sulfate, and ultrasonically disperse in an ultrasonic cell pulverizer for 40 minutes, Then it was magnetically stirred in a constant temperature water bath at 35° C. at a stirring rate of 800 rpm for 30 minutes to obtain a uniform core material emulsion (A).
[0034] (2) Add 6-8 mL of tetraethyl orthosilicate to 25 mL of cyclohexane, and keep stirring for 30 minutes at a speed of 600-1000 rpm in a magnetic stirrer, then add 5 mL of amyl alcohol dropwise under stirring , and then continued to stir for 10 minutes at the same rotating speed to obtain a transparent prepolymer solution (B).
[0035](3) Add the uniformly dispersed core material emulsion (A) dropwise to the transparent prepolymer solution (B), keep a constant temperature at 60°C, and magnetically stir at a speed of 600-1000rpm for 30 minutes to form a uniformly dispersed so...
Embodiment 2
[0037] (1) Weigh 12g of sodium acetate trihydrate, dissolve it in 15mL of deionized water to form a solution, add 0.6-0.8g of sodium dodecylbenzenesulfonate, and ultrasonically disperse in an ultrasonic cell pulverizer for 30 minutes, and then magnetically stirred in a constant temperature water bath at 40° C. at a stirring rate of 600 rpm for 40 minutes to obtain a uniform core material emulsion (A).
[0038] (2) Add 8-10 mL of sodium silicate solution into 30 mL of ethanol, and continue stirring for 30 minutes at a speed of 600-1000 rpm in a magnetic stirrer to obtain a transparent prepolymer solution (B).
[0039] (3) Add the uniformly dispersed core material emulsion (A) dropwise to the transparent prepolymer solution (B), keep a constant temperature at 50°C, and magnetically stir at a speed of 600-1000rpm for 30 minutes to form a uniformly dispersed solution, Then, hydrochloric acid was added dropwise during the stirring process to adjust the pH value of the solution to 9...
PUM
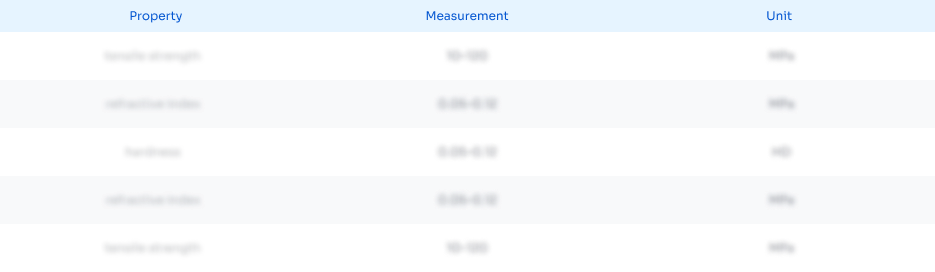
Abstract
Description
Claims
Application Information

- R&D
- Intellectual Property
- Life Sciences
- Materials
- Tech Scout
- Unparalleled Data Quality
- Higher Quality Content
- 60% Fewer Hallucinations
Browse by: Latest US Patents, China's latest patents, Technical Efficacy Thesaurus, Application Domain, Technology Topic, Popular Technical Reports.
© 2025 PatSnap. All rights reserved.Legal|Privacy policy|Modern Slavery Act Transparency Statement|Sitemap|About US| Contact US: help@patsnap.com