Rubber water-stopping belt and preparation method thereof
A technology of rubber waterstop and softening plasticizer, which is applied in the field of waterstop and its preparation, and can solve the problems of difficult control of cross-linked saturated CPE rubber production, poor tear resistance and liquid permeability, and large compression permanent deformation, etc. Problems, achieve the effect of reducing energy consumption, high resistance to liquid penetration, and small compression permanent deformation
- Summary
- Abstract
- Description
- Claims
- Application Information
AI Technical Summary
Problems solved by technology
Method used
Image
Examples
Embodiment 1
[0020] (1) In parts by weight, 100 parts of chlorinated polyethylene, 35 parts of dioctyl phthalate, 5 parts of magnesium oxide, 1 part of paraffin, 45 parts of carbon black, kaolin 25 parts, 1 part of zinc oxide, and 1 part of stearic acid were put into the internal mixer in order to mix the rubber for 5 minutes. The temperature of the internal mixing was 100°C. 4~5mm output film;
[0021] (2) Put the obtained film into the internal mixer, add 5 parts of diethylthiourea and 1.5 parts of sulfur and mix for 1 minute to remove the glue, the temperature is 80 ° C, and then return to the glue on the mixer for 3 minutes, and press it into a sheet semi-finished film;
[0022] (3) The obtained semi-finished mixed rubber sheet is molded into a finished waterstop by a vulcanizing machine, the vulcanization pressure is 10 MPa, the vulcanization temperature is 165° C., and the vulcanization time is 18 minutes.
Embodiment 2
[0024] (1) In parts by weight, the raw material chlorine content is 100 parts of chlorinated polyethylene, 25 parts of dioctyl phthalate, 5 parts of dioctyl sebacate, and 5 parts of epoxidized soybean oil , 8 parts of magnesium hydroxide, 1 part of paraffin wax, 1 part of polyethylene wax, 35 parts of carbon black, 10 parts of white carbon black, 25 parts of calcium carbonate, 3 parts of zinc oxide, 1 part of stearic acid, put into banburying in order The rubber is mixed in the machine for 5 minutes, the mixing temperature is 100°C, after the glue is discharged, the rubber is returned to the open mill for 5 minutes, and the roller distance is adjusted to 4-5mm to produce the film;
[0025] (2) Put the obtained film into the internal mixer, add 10 parts of diethylthiourea and 2.0 parts of sulfur and mix for 1 minute to remove the glue, the temperature is 80 ° C, and then return to the glue on the mixer for 3 minutes, and press it into a sheet semi-finished film;
[0026] (3) T...
Embodiment 3
[0028] (1) In parts by weight, the raw material chlorine content is 100 parts of chlorinated polyethylene, 40 parts of dioctyl phthalate, 10 parts of magnesium oxide, 1 part of paraffin wax, 1 part of polyethylene wax, 1 part of calcium stearate, 45 parts of carbon black, 15 parts of kaolin, 15 parts of talcum powder, 1 part of zinc oxide, and 1 part of stearic acid are put into the internal mixer in order to mix rubber for 8 minutes, and the mixing temperature is 105 ℃, after debinding, return to the glue on the open mill for 8 minutes, and adjust the roller distance to 4-5mm to release the film;
[0029] (2) Put the obtained film into the internal mixer, add 6 parts of diethylthiourea and 1.0 part of sulfur and mix for 2 minutes to remove the glue, the temperature is 90 ° C, and then return to the glue on the mixer for 5 minutes, and press it into a sheet semi-finished film;
[0030] (3) The obtained semi-finished mixed film is extruded through an extruder to form a mold, a...
PUM
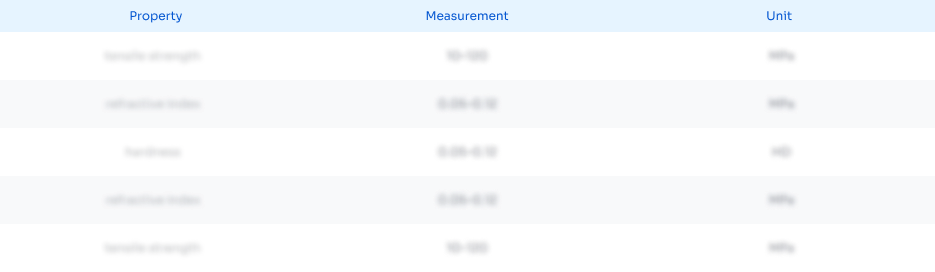
Abstract
Description
Claims
Application Information

- R&D
- Intellectual Property
- Life Sciences
- Materials
- Tech Scout
- Unparalleled Data Quality
- Higher Quality Content
- 60% Fewer Hallucinations
Browse by: Latest US Patents, China's latest patents, Technical Efficacy Thesaurus, Application Domain, Technology Topic, Popular Technical Reports.
© 2025 PatSnap. All rights reserved.Legal|Privacy policy|Modern Slavery Act Transparency Statement|Sitemap|About US| Contact US: help@patsnap.com