Process for improving full mold casting engine cylinder yield
A technology of engine cylinder block and lost foam casting, which is applied in the direction of casting molding equipment, casting mold components, manufacturing tools, etc. It can solve the problems of reducing cleaning, saving machining internal defects, affecting the yield of engine cylinder block, and difficult fixing of quartz sand, etc. problems, to achieve the effect of ensuring pouring stability, increasing viscosity, and preventing sand collapse
- Summary
- Abstract
- Description
- Claims
- Application Information
AI Technical Summary
Problems solved by technology
Method used
Examples
Embodiment 1
[0020] A process for improving the yield rate of lost foam casting engine cylinders includes the following steps:
[0021] S1. Molding. Install a foamed plastic mold with the same size and shape as the casting size and shape in the sand box. Use expandable methyl methacrylate and styrene copolymer resin beads to convert the expandable The proportion of methyl acrylate and styrene copolymer resin beads is injected into the steam foaming machine at a ratio of 85%: 15% for foam molding;
[0022] S2. Combination: Combine and bond the molded foam model and the pouring riser model to form an engine block model cluster;
[0023] S3. Coating. The model clusters are coated with special paint by immersion method. The coated model clusters are dried by air drying equipment at 50℃, and the coating thickness is controlled at 2mm, according to the size of the engine block casting Thickness control to make the lost foam model;
[0024] S4. Forming. Put the lost foam model into the sand box to fill ...
Embodiment 2
[0030] A process for improving the yield rate of lost foam casting engine cylinders includes the following steps:
[0031] S1. Molding. Install a foamed plastic mold with the same size and shape as the casting size and shape in the sand box. Use expandable methyl methacrylate and styrene copolymer resin beads to convert the expandable The proportion of methyl acrylate and styrene copolymer resin beads is injected into the steam foaming machine at a ratio of 90%: 10% for foam molding;
[0032] S2. Combination: Combine and bond the molded foam model and the pouring riser model to form an engine block model cluster;
[0033] S3. Coating. The model clusters are coated with special paint by immersion method. The coated model clusters are dried by air drying equipment at 45℃. The coating thickness is controlled at 1.8mm, according to the size of the engine block casting Carry out thickness control to make the lost foam model;
[0034] S4. Forming. Put the lost foam model into the sand box ...
PUM
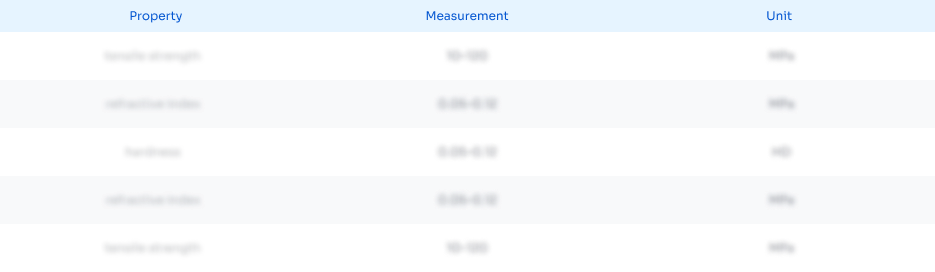
Abstract
Description
Claims
Application Information

- R&D
- Intellectual Property
- Life Sciences
- Materials
- Tech Scout
- Unparalleled Data Quality
- Higher Quality Content
- 60% Fewer Hallucinations
Browse by: Latest US Patents, China's latest patents, Technical Efficacy Thesaurus, Application Domain, Technology Topic, Popular Technical Reports.
© 2025 PatSnap. All rights reserved.Legal|Privacy policy|Modern Slavery Act Transparency Statement|Sitemap|About US| Contact US: help@patsnap.com