Wearproof ceramic tile and preparation method thereof
A technology of ceramic tiles and ceramics, which is applied in the field of preparation of wear-resistant ceramic tiles and wear-resistant ceramic tiles. Glossy surface, not easy to hide dirt
- Summary
- Abstract
- Description
- Claims
- Application Information
AI Technical Summary
Problems solved by technology
Method used
Examples
preparation example Construction
[0048] Correspondingly, the present invention also provides a preparation method of wear-resistant ceramic tiles, comprising the following steps:
[0049] Step 1: Mix kaolin, ceramic waste, calcined quartz stone, bauxite, brown corundum, talcum powder, clay and methyl cellulose according to the proportion, put them in a ball mill and mill them for 40-80 minutes to obtain a mixture;
[0050] Step 2: Add 0.1-2 parts by weight of yellow dextrin to the mixture, and add water to knead and slurry to obtain a slurry;
[0051] Step 3: Spray-dry the slurry to granules with a water content of 4-6%;
[0052] Step 4: put the spray-dried material in step 3 into a molding machine and press it under a pressure of 65-75MPa to obtain a wet billet;
[0053] Step 5: drying the wet billet at 50°C-150°C for 20-30 hours to obtain a dry billet;
[0054] Step 6: After printing on the dry blank, send it to the roller kiln for firing to obtain the finished product.
Embodiment 1
[0057] Step 1: Mix 24 parts of kaolin, 28 parts of ceramic waste, 20 parts of calcined quartz stone, 12 parts of bauxite, 5 parts of brown corundum, 6 parts of talcum powder, 7 parts of clay and 2 parts of methyl cellulose according to the proportion, set Ball milled in a ball mill for 60 minutes to obtain a mixture;
[0058] Step 2: Add 0.5 parts by weight of yellow dextrin to the mixture, and add water to knead and slurry to obtain a slurry;
[0059] Step 3: Spray-dry the slurry to granules with a water content of 4%;
[0060] Step 4: Put the spray-dried material in step 3 into a molding machine and press it under a pressure of 70MPa to obtain a wet billet;
[0061] Step 5: drying the wet billet at 80°C for 25 hours to obtain a dry billet;
[0062] Step 6: After printing on the dry blank, send it to the roller kiln for firing to obtain the finished product.
[0063] After testing, it is found that the wear of ceramic tiles in long-term use at room temperature is ≤3cm 3 ,...
Embodiment 2
[0065] Step 1: Mix 19 parts of kaolin, 32 parts of ceramic waste, 30 parts of calcined quartz stone, 15 parts of bauxite, 4 parts of brown corundum, 8 parts of talcum powder, 8 parts of clay and 3 parts of methyl cellulose according to the proportion, set Ball milled in a ball mill for 80 minutes to obtain a mixture;
[0066] Step 2: Add 2 parts by weight of yellow dextrin to the mixture, and add water to knead and slurry to obtain a slurry;
[0067] Step 3: Spray-dry the slurry to 6% granules;
[0068] Step 4: Put the spray-dried material in step 3 into a molding machine and press it under a pressure of 75MPa to obtain a wet billet;
[0069] Step 5: drying the wet billet at 100°C for 28 hours to obtain a dry billet;
[0070] Step 6: After printing on the dry blank, send it to the roller kiln for firing to obtain the finished product.
[0071] After testing, it is found that the wear of ceramic tiles in long-term use at room temperature is ≤5cm3 , the product has high wear ...
PUM
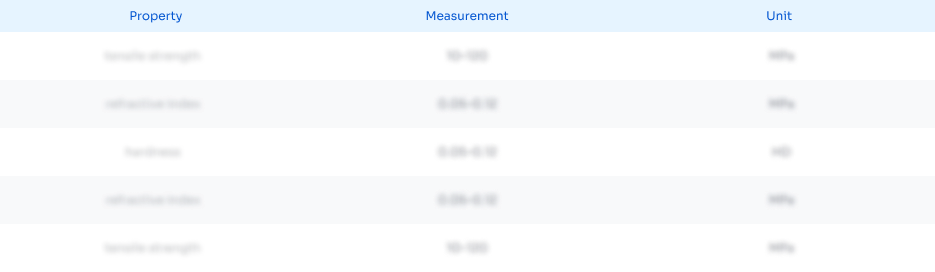
Abstract
Description
Claims
Application Information

- R&D
- Intellectual Property
- Life Sciences
- Materials
- Tech Scout
- Unparalleled Data Quality
- Higher Quality Content
- 60% Fewer Hallucinations
Browse by: Latest US Patents, China's latest patents, Technical Efficacy Thesaurus, Application Domain, Technology Topic, Popular Technical Reports.
© 2025 PatSnap. All rights reserved.Legal|Privacy policy|Modern Slavery Act Transparency Statement|Sitemap|About US| Contact US: help@patsnap.com