Braking drum with bionic non-smooth surface
A non-smooth surface, brake drum technology, applied in the direction of brake drum, etc., to achieve the effect of not easy to scratch, improve wear resistance, and increase production cost
- Summary
- Abstract
- Description
- Claims
- Application Information
AI Technical Summary
Problems solved by technology
Method used
Image
Examples
Embodiment 1
[0038] Fabrication of heavy duty truck brake drums with convex non-smooth morphology on the surface.
[0039] refer to figure 1, the surface of the brake drum is machined with a laser to have a convex-hull non-smooth surface, the height difference between the non-smooth unit body and the surface of the brake drum base is 0.5 mm, the diameter of the bottom circle d is 4 mm, and the center distance s of the unit body is 50mm. The material of the brake drum is HT250 gray iron, the friction coefficient is 0.37, and the hardness is HB175.
[0040] After processing, the various indicators of the non-smooth unit body are tested as friction coefficient: 0.67, hardness: HB520, friction coefficient increased by 0.30, hardness increased by HB345, and the service life of the brake drum with bionic non-smooth surface is longer than that of the smooth surface of the same substrate. Drums are doubled, while the cost of dealing with biomimetic non-smooth surfaces is only increased by 5%.
Embodiment 2
[0042] Manufacture of heavy duty truck brake drums with dimpled non-smooth morphology on the surface.
[0043] refer to figure 2 , the surface of the brake drum is processed into a pit-shaped non-smooth surface with a laser, the height difference between the non-smooth unit body and the surface of the brake drum base is 0.5mm, the diameter d of the upper opening of the pit is 4mm, and the distance between the center of the unit body is s is 50mm. The material of the brake drum is HT250 gray iron, the friction coefficient is 0.37, and the hardness is HB175.
[0044] After processing, the various indicators of the non-smooth unit body are tested as friction coefficient: 0.67, hardness: HB518, friction coefficient increased by 0.30, hardness increased by HB343, and the service life of the brake drum with bionic non-smooth surface is longer than that of the smooth surface of the same substrate. Drums are doubled, while the cost of dealing with biomimetic non-smooth surfaces is ...
Embodiment 3
[0046] Manufacture of heavy duty truck brake drums with striated non-smooth morphology on the surface.
[0047] refer to image 3 , the surface of the brake drum is processed into a striped non-smooth surface by laser, the height difference between the non-smooth unit body and the surface of the brake drum base is 0.5 mm, the width w is 3 mm, the center distance s of the unit body is 40 mm, and the inclination angle α is about 45°. The material of the brake drum is HT250 gray iron, the friction coefficient is 0.37, and the hardness is HB175.
[0048] After processing, the indicators of the non-smooth unit body are tested as friction coefficient: 0.70, hardness: HB532, friction coefficient increased by 0.33, hardness increased by HB357, and the service life of the brake drum with bionic non-smooth surface is longer than that of the smooth surface of the same substrate. The drum is 1.2 times higher, while the cost of processing bionic non-smooth surfaces is only 8% higher.
PUM
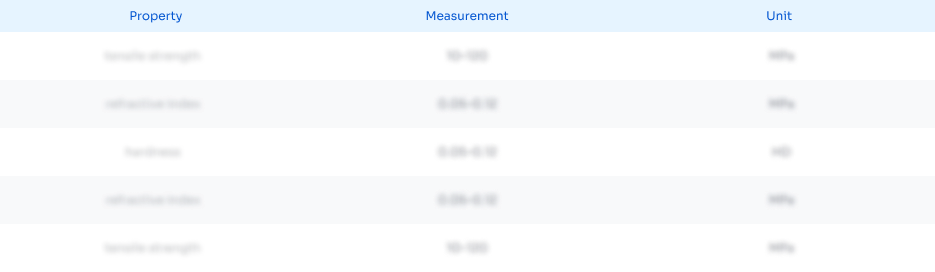
Abstract
Description
Claims
Application Information

- R&D
- Intellectual Property
- Life Sciences
- Materials
- Tech Scout
- Unparalleled Data Quality
- Higher Quality Content
- 60% Fewer Hallucinations
Browse by: Latest US Patents, China's latest patents, Technical Efficacy Thesaurus, Application Domain, Technology Topic, Popular Technical Reports.
© 2025 PatSnap. All rights reserved.Legal|Privacy policy|Modern Slavery Act Transparency Statement|Sitemap|About US| Contact US: help@patsnap.com