Machining technology for metal ceramic flange
A processing technology and cermet technology, which is applied in the field of processing technology using cermet flanges, can solve problems such as burden, increase in overall weight, dust explosion, etc., and achieve the effects of reducing grinding, reducing working time, and increasing stability.
- Summary
- Abstract
- Description
- Claims
- Application Information
AI Technical Summary
Problems solved by technology
Method used
Examples
Embodiment Construction
[0019] In order to make the technical means, creative features, goals and effects achieved by the present invention easy to understand, the present invention will be further described below in conjunction with specific embodiments.
[0020] A processing technique for a cermet flange, characterized in that it comprises the following steps:
[0021] In the first step, add the powdered raw materials into the container according to the weight ratio, then stir evenly, and then add an appropriate amount of water to stir the powdery raw materials in the container evenly;
[0022] In the second step, first coat a layer of release agent on the surface of the inner wall of the mold for making the flange, fill the raw material mixed with water into the mold, and press the raw material in the mold with a pressure plate;
[0023] The third step is to heat the mold to evaporate the water in the flange, and then press the flange in the mold after the water evaporates;
[0024] The fourth st...
PUM
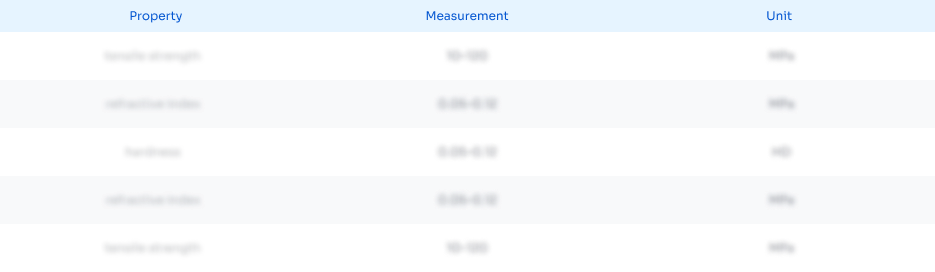
Abstract
Description
Claims
Application Information

- R&D Engineer
- R&D Manager
- IP Professional
- Industry Leading Data Capabilities
- Powerful AI technology
- Patent DNA Extraction
Browse by: Latest US Patents, China's latest patents, Technical Efficacy Thesaurus, Application Domain, Technology Topic, Popular Technical Reports.
© 2024 PatSnap. All rights reserved.Legal|Privacy policy|Modern Slavery Act Transparency Statement|Sitemap|About US| Contact US: help@patsnap.com