Wear-resistant anti-cracking cable material and preparation method thereof
A cable material and anti-cracking technology, which is applied in the direction of insulating cables, cables, circuits, etc., can solve the problems that the mechanical properties, processing properties and flame-retardant properties cannot be balanced, and cannot completely solve the problems of the combination of inorganic flame-retardant fillers and plastics, and achieve Effects of improving mechanical properties, preventing cracking, and improving flame retardancy
- Summary
- Abstract
- Description
- Claims
- Application Information
AI Technical Summary
Problems solved by technology
Method used
Examples
Embodiment Construction
[0014] A wear-resistant and anti-cracking cable material, which is made of the following raw materials in parts by weight (kg): nano-titanium dioxide 3.5, pitch 3.5, zirconium silicate 7, aluminum hydroxide 6.5, polyacrylonitrile 9.5, polylactic acid 6.5, polyethylene oxide 3.5. Appropriate amount of dimethylformamide, appropriate amount of composite solvent with a volume ratio of dimethylformamide / dichloromethane of 1:1, appropriate amount of methyl methacrylate, appropriate amount of isopropyl thioxanthone, and ethylene-vinyl acetate copolymer 23. Low-density polyethylene 83.
[0015] The production method of the wear-resistant and anti-cracking cable material is characterized in that:
[0016] (1) Dissolve polyacrylonitrile in dimethylformamide to make a 12wt% solution, and dissolve polylactic acid in a composite solvent with a volume ratio of dimethylformamide / dichloromethane of 1:1 to make a 11wt% solution The solution, polyoxyethylene is dissolved in dimethylformamide / d...
PUM
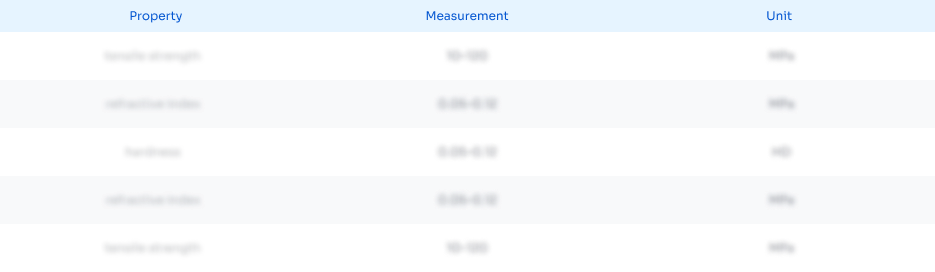
Abstract
Description
Claims
Application Information

- R&D Engineer
- R&D Manager
- IP Professional
- Industry Leading Data Capabilities
- Powerful AI technology
- Patent DNA Extraction
Browse by: Latest US Patents, China's latest patents, Technical Efficacy Thesaurus, Application Domain, Technology Topic, Popular Technical Reports.
© 2024 PatSnap. All rights reserved.Legal|Privacy policy|Modern Slavery Act Transparency Statement|Sitemap|About US| Contact US: help@patsnap.com