Preparation technology of furfural
A furfural and process technology, applied in the field of furfural preparation process, to achieve the effects of saving volume, eliminating excessive reaction, and enhancing microscopic mixing effect
- Summary
- Abstract
- Description
- Claims
- Application Information
AI Technical Summary
Problems solved by technology
Method used
Image
Examples
Embodiment 1
[0053] The crushed corn stalks and water were injected into the hydrolysis tank according to the mass ratio of 1:1. The pre-hydrolysis temperature was 160°C and the pre-hydrolysis time was 30 min. The mass concentrations of pentose, acetic acid and formic acid in the pentose solution obtained after the reaction were 5.2% and 2.5% respectively. , 0.7%.
[0054] The composite extractant used is dimethyl phthalate, n-octanol, ethyl triphenylphosphine hexafluorophosphate mixed solvent, wherein, dimethyl phthalate accounts for 40wt%, n-octanol accounts for 20wt%, Ethyl triphenylphosphine hexafluorophosphate accounts for 40wt%.
[0055] The feed ratio of extractant and pentose solution is 3:1 (volume ratio), and the feed rate of extractant and pentose solution is equal to the impinging flow reactor volume (that is, the feed volume space velocity is 1h -1 , that is, the reaction time is 1h), and the circulating material rate is 200% of the feed amount. Control the reaction temperat...
Embodiment 2
[0058] According to the method of Example 1, the difference is that the feed rate is twice the volume of the impinging flow reactor, that is, the reaction time is 0.5 h.
[0059] The experimental results showed that the conversion rate of pentose sugar was 77wt%, the yield of furfural was 60.9wt%, the recovery rate of acetic acid was 94.1wt%, and the recovery rate of formic acid was 90.7wt%.
Embodiment 3
[0061] According to the method of Example 1, the difference is that the feed rate is 0.67 times the volume of the impinging flow reactor, that is, the reaction time is 1.5 h.
[0062] The experimental results showed that the conversion rate of pentose sugar was 99%, the yield of furfural was 82.4%, the recovery rate of acetic acid was 94.1%, and the recovery rate of formic acid was 90.7%.
PUM
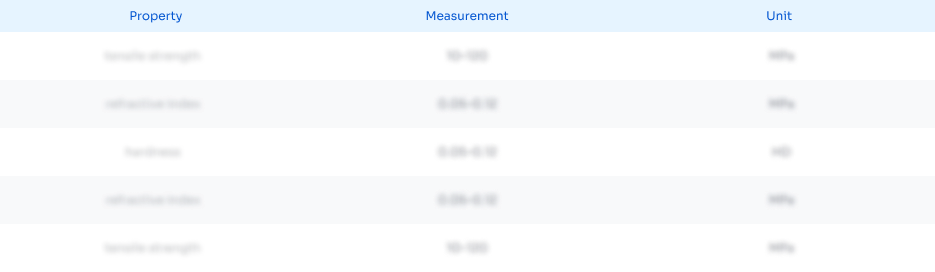
Abstract
Description
Claims
Application Information

- R&D Engineer
- R&D Manager
- IP Professional
- Industry Leading Data Capabilities
- Powerful AI technology
- Patent DNA Extraction
Browse by: Latest US Patents, China's latest patents, Technical Efficacy Thesaurus, Application Domain, Technology Topic, Popular Technical Reports.
© 2024 PatSnap. All rights reserved.Legal|Privacy policy|Modern Slavery Act Transparency Statement|Sitemap|About US| Contact US: help@patsnap.com