Light emitting diode having full mirror surface structure and manufacturing method therefor
A technology for light-emitting diodes and a manufacturing method, which is applied to electrical components, circuits, semiconductor devices, etc., can solve problems such as loss of mirror surface area and brightness loss, and achieve the effects of improving yield, increasing area, and simplifying processes
- Summary
- Abstract
- Description
- Claims
- Application Information
AI Technical Summary
Problems solved by technology
Method used
Image
Examples
Embodiment Construction
[0026] The core point of the present invention is to provide an LED structure with a full mirror structure, which uses epitaxy to grow the DBR layer in advance, removes the DBR layer in the light-transmitting area in the chip process, and only retains the DBR in the ohmic contact electrode area, so that the ohmic contact electrode area It can not only form ohmic contact but also has the effect of reflecting layer. The present invention will be further described below in conjunction with the drawings and preferred specific embodiments.
[0027] Please see figure 2 According to the implementation of the present invention, a light-emitting diode with a total reflection structure, from bottom to top, includes: a conductive substrate 202, a metal bonding layer 280, a metal reflective layer 270, a light-transmitting layer 260, a light-emitting epitaxial stack 240, and P Type electrode 290.
[0028] Specifically, the conductive substrate 202 can be a Si substrate, a metal substrate, or ...
PUM
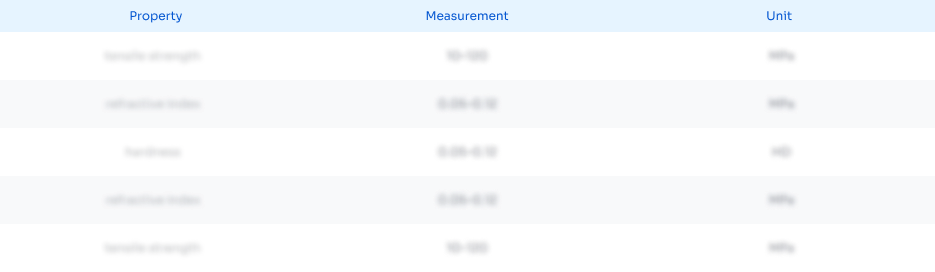
Abstract
Description
Claims
Application Information

- R&D
- Intellectual Property
- Life Sciences
- Materials
- Tech Scout
- Unparalleled Data Quality
- Higher Quality Content
- 60% Fewer Hallucinations
Browse by: Latest US Patents, China's latest patents, Technical Efficacy Thesaurus, Application Domain, Technology Topic, Popular Technical Reports.
© 2025 PatSnap. All rights reserved.Legal|Privacy policy|Modern Slavery Act Transparency Statement|Sitemap|About US| Contact US: help@patsnap.com