Flame-retardant cable insulating material containing nanometer perovskite oxide and application
A technology of insulating materials and flame-retardant cables, which is applied in the direction of insulators, insulated conductors, and insulated cables, can solve the problems of unsatisfactory flame-retardant performance, and achieve the goals of improving energy-saving performance, increasing anti-aging, and increasing loss-on-ignition index Effect
- Summary
- Abstract
- Description
- Claims
- Application Information
AI Technical Summary
Problems solved by technology
Method used
Examples
Embodiment 1
[0036] (1) Preparation of BaTiO 3 With ZIF-90:
[0037] (a) Preparation of nano-titanate template: 0.1mol / l tetraisobutyl titanate was dissolved in 10ml ethylene glycol monomethyl ether, ultrasonically dispersed, stirred evenly, and 25% ammonia water was added to obtain titanium hydroxide precipitation, Deionized wash. Then add 1mol / l KOH aqueous solution, stir for 10-20 minutes, mix well, transfer to a hydrothermal crystallization kettle, and react at 140-200°C for 1-4h. After the reaction is finished, wash and dry to obtain a nano-titanate template;
[0038] Add 15ml of barium nitrate solution with a concentration of 0.2mol / l and 10ml of an aqueous solution of tetramethylammonium hydroxide with a concentration of 0.1mol / l to 2g of nano-titanate nano-template, stir for 2h, mix well, and then carry out 180-220°C hydrothermal reaction for 1-4h, then cooling and precipitation. The finally obtained product was washed with deionized water and methanol respectively. BaTiO 3 T...
Embodiment 2
[0042] (1) Preparation of SrTiO 3 With ZIF-90:
[0043] (a) Preparation of nano-titanate template: 0.3mol / l tetraisobutyl titanate was dissolved in 10ml ethylene glycol monomethyl ether, ultrasonically dispersed, stirred evenly, and 25wt% ammonia water was added to obtain titanium hydroxide precipitation, Deionized wash. Then add 2mol / l KOH aqueous solution, stir for 10-20 minutes, mix evenly, transfer to a hydrothermal crystallization kettle, and react at 140-200°C for 1-4h. After the reaction is finished, wash and dry to obtain a nano-titanate template;
[0044] Add 20ml of strontium nitrate solution with a concentration of 0.2mol / l and 10ml of an aqueous solution of tetramethylammonium hydroxide with a concentration of 0.1mol / l to 2g of nano titanate template, and stir for 2 hours. Thermal reaction for 4h, then cooling and precipitation. The finally obtained product was washed with deionized water and methanol respectively. The size of the product SrTiO3 is 40-60nm.
...
Embodiment 3
[0048] (1) Preparation of CaTiO 3 With ZIF-90:
[0049] (a) Preparation of nano-titanate template: 0.5mol / l tetraisobutyl titanate was dissolved in 10ml ethylene glycol monomethyl ether, ultrasonically dispersed, stirred evenly, and 25wt% ammonia water was added to obtain titanium hydroxide precipitation, Deionized wash. Then add 1mol / l KOH aqueous solution, stir for 10-20 minutes, mix well, transfer to a hydrothermal crystallization kettle, and react at 200°C for 3h. After the reaction is finished, wash and dry to obtain a nano-titanate template;
[0050] Add 15ml of 0.5mol / l calcium nitrate solution and 15ml of 0.3mol / l tetramethylammonium hydroxide aqueous solution to 3g of nano titanate template, stir for 2h, mix well, and then carry out 180℃ water Thermal reaction for 4h, then cooling and precipitation. The finally obtained product was washed with deionized water and methanol respectively. ProductCaTiO 3 The average diameter is 35-55nm.
[0051] (b) Preparation of ...
PUM
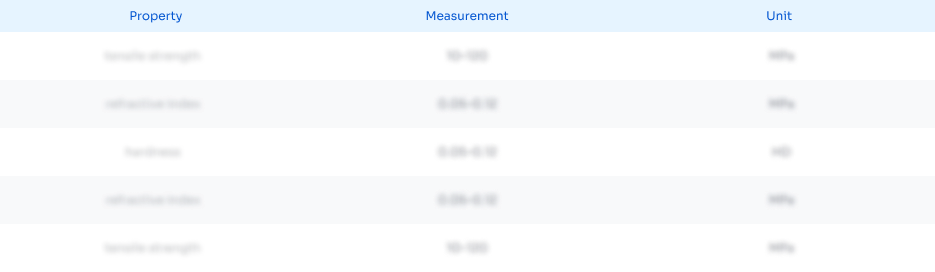
Abstract
Description
Claims
Application Information

- R&D
- Intellectual Property
- Life Sciences
- Materials
- Tech Scout
- Unparalleled Data Quality
- Higher Quality Content
- 60% Fewer Hallucinations
Browse by: Latest US Patents, China's latest patents, Technical Efficacy Thesaurus, Application Domain, Technology Topic, Popular Technical Reports.
© 2025 PatSnap. All rights reserved.Legal|Privacy policy|Modern Slavery Act Transparency Statement|Sitemap|About US| Contact US: help@patsnap.com