Five-phase permanent-magnet embedded fault-tolerant linear-motor non-adjacent two-phase fault-tolerant vector control method
A linear motor, vector control technology, applied in motor control, vector control system, motor generator control and other directions, can solve the problems of motor response speed drop, serious noise, poor dynamic performance, etc., to achieve constant switching frequency, low CPU overhead , the effect of suppressing thrust fluctuations
- Summary
- Abstract
- Description
- Claims
- Application Information
AI Technical Summary
Problems solved by technology
Method used
Image
Examples
Embodiment Construction
[0040] The following will clearly and completely describe the technical solutions in the embodiments of the present invention with reference to the drawings in the embodiments of the present invention.
[0041] In order to more simply and clearly illustrate the structural features and beneficial effects of the permanent magnet embedded fault-tolerant linear motor of the present invention, a detailed description will be given below in conjunction with a specific five-phase permanent magnet embedded fault-tolerant linear motor.
[0042] Step 1, establish a five-phase permanent magnet embedded fault-tolerant linear motor model;
[0043] Such as figure 1 As shown, the structure diagram of the five-phase permanent magnet embedded fault-tolerant linear motor according to the embodiment of the present invention includes primary 1 and secondary 2 . The primary 1 includes pole shoes 4, armature teeth 6, fault-tolerant teeth 5 and concentrated winding coils 9, and there are 10 armature...
PUM
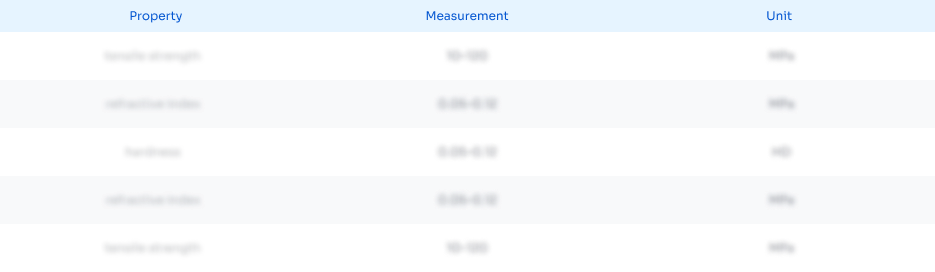
Abstract
Description
Claims
Application Information

- Generate Ideas
- Intellectual Property
- Life Sciences
- Materials
- Tech Scout
- Unparalleled Data Quality
- Higher Quality Content
- 60% Fewer Hallucinations
Browse by: Latest US Patents, China's latest patents, Technical Efficacy Thesaurus, Application Domain, Technology Topic, Popular Technical Reports.
© 2025 PatSnap. All rights reserved.Legal|Privacy policy|Modern Slavery Act Transparency Statement|Sitemap|About US| Contact US: help@patsnap.com