Method for preparing nitrile rubber filled with carbon nano tube and having thermal-oxidative aging resistance
A technology of carbon nanotubes and nitrile rubber, which is applied in the field of rubber, can solve problems such as few reports, and achieve the effects of simple and easy preparation process, excellent high temperature resistance, and strong process operability
- Summary
- Abstract
- Description
- Claims
- Application Information
AI Technical Summary
Problems solved by technology
Method used
Image
Examples
Embodiment 1
[0047] (1) Preparation of functional carbon nanotubes
[0048] Weigh 13 g of multi-walled carbon nanotubes, and simultaneously measure 450 mL of concentrated sulfuric acid and 150 mL of concentrated nitric acid into a 1000 mL beaker, stir mechanically for 30 min, transfer the mixture to a 1000 mL three-necked flask, and reflux at 120 °C for 6 h. After the temperature in the flask dropped to room temperature, the activated carbon nanotubes were centrifuged and washed with a large amount of distilled water until neutral, and placed in a vacuum drying oven at 80° C. for 24 hours. The mass concentrations of concentrated sulfuric acid and concentrated nitric acid are 98% and 68% respectively.
[0049] Weigh 10 g of activated carbon nanotubes, 5 g of hindered phenol AO-80, and 600 mL of solvent DMF, put them in a 1000 mL beaker, stir mechanically for 30 min, transfer the mixture to a 1000 mL three-necked flask, and reflux at 160 °C for 10 h. After the temperature in the flask dropp...
Embodiment 2
[0058] (1) Preparation of functional carbon nanotubes
[0059] The preparation method of functional carbon nanotubes is the same as that in Example 1.
[0060] (2) Preparation of nitrile rubber
[0061] 100 parts of nitrile rubber (40% by mass of acrylonitrile) raw rubber was masticated on an open mill and rolled several times. Reduce the roller pitch, and mix 30 parts of hindered phenol-modified carbon nanotubes, 3 parts of magnesium stearate, 2 parts of zinc oxide, 2.5 parts of sulfur and 1 part of accelerator TMTD on the open mill. The mixed rubber was vulcanized in a hot press, and hot-pressed at 15MPa and 160°C for 30min to obtain the final product.
[0062] The performance data of the prepared nitrile rubber is shown in Table 2.
Embodiment 3
[0064] 1. Preparation of functional carbon nanotubes
[0065] The preparation steps of functional carbon nanotubes are the same as Example 1.
[0066] 2. Preparation of NBR
[0067] 100 parts of nitrile rubber (40% by mass of acrylonitrile) raw rubber was masticated on an open mill and rolled several times. Reduce the roller distance, mix 15 parts of hindered phenol modified carbon nanotubes, 3 parts of calcium hydroxide, 2 parts of zinc stearate, 2.5 parts of sulfur, 1 part of accelerator DM and 0.5 parts of accelerator TMTD on the open mill uniform. The mixed rubber was vulcanized in a hot press, and hot pressed at 20 MPa and 155° C. for 30 minutes to obtain the final product.
[0068] The performance data of the prepared nitrile rubber is shown in Table 2.
PUM
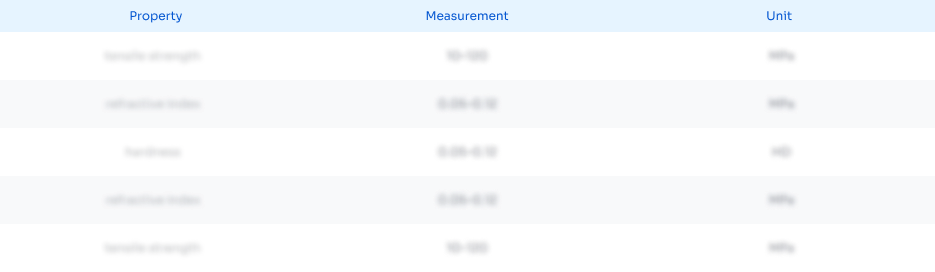
Abstract
Description
Claims
Application Information

- Generate Ideas
- Intellectual Property
- Life Sciences
- Materials
- Tech Scout
- Unparalleled Data Quality
- Higher Quality Content
- 60% Fewer Hallucinations
Browse by: Latest US Patents, China's latest patents, Technical Efficacy Thesaurus, Application Domain, Technology Topic, Popular Technical Reports.
© 2025 PatSnap. All rights reserved.Legal|Privacy policy|Modern Slavery Act Transparency Statement|Sitemap|About US| Contact US: help@patsnap.com