Circuit layout structure of wireless data transmitting-receiving sensor used for measuring clamping force of chuck
A sensor circuit and wireless data technology, applied in the direction of measuring/indicating equipment, metal processing machinery parts, metal processing equipment, etc., can solve the problems of large measurement error, large interference noise, and small measurement value, etc., to achieve accurate measurement, The effect of accurate data sending and receiving and stable performance
- Summary
- Abstract
- Description
- Claims
- Application Information
AI Technical Summary
Problems solved by technology
Method used
Image
Examples
Embodiment
[0030] In an embodiment of the present invention, a sensor circuit layout structure for measuring clamping force includes: wireless data transmission circuit layout ( figure 1 ) and wireless data receiving circuit layout ( figure 2 ) consists of two main bodies.
[0031] Such as figure 1 As shown, the wireless data transmission circuit layout consists of the main controller module in the first layout area, the power supply module in the second layout area, the wireless communication transmission module in the third layout area, the data signal conditioning module in the fourth layout area and the third layout area. 5 The speed measurement module in the layout area. The 1st and 2nd layout areas are connected to all other layout areas, the 3rd layout area is connected to the 1st and 2nd layout areas, the 4th layout area is connected to the 1st and 2nd layout areas, and the 5th layout area is connected to the 1st and 2nd layout areas connected.
[0032] Embodiment, wireless ...
PUM
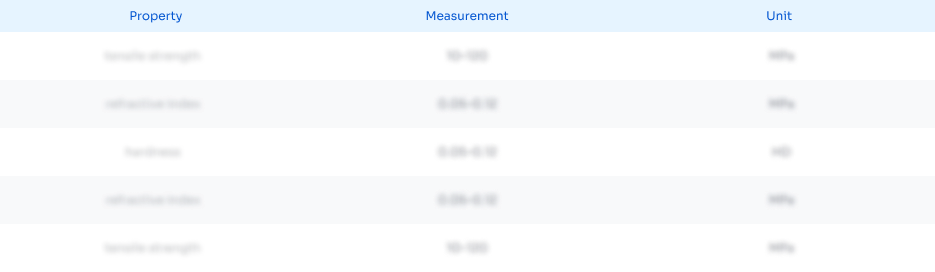
Abstract
Description
Claims
Application Information

- R&D
- Intellectual Property
- Life Sciences
- Materials
- Tech Scout
- Unparalleled Data Quality
- Higher Quality Content
- 60% Fewer Hallucinations
Browse by: Latest US Patents, China's latest patents, Technical Efficacy Thesaurus, Application Domain, Technology Topic, Popular Technical Reports.
© 2025 PatSnap. All rights reserved.Legal|Privacy policy|Modern Slavery Act Transparency Statement|Sitemap|About US| Contact US: help@patsnap.com