Molybdenum phenolic resin precoated sand material for instrument casting
A technology of molybdenum phenolic resin and coated sand, which is applied in the direction of casting molding equipment, casting molds, manufacturing tools, etc., can solve the problems that it is difficult to meet the actual casting performance and the high performance requirements of coated sand, so as to increase the universality , Improve the yield and delay the gas generation speed
- Summary
- Abstract
- Description
- Claims
- Application Information
AI Technical Summary
Problems solved by technology
Method used
Examples
Embodiment 1
[0012] Embodiment 1: a molybdenum phenolic resin coated sand material for instrument casting, including the following raw materials in parts by weight: 1.5 parts of molybdenum phenolic resin, 0.04 part of coupling agent, 0.4 part of urotropine, 0.3 part of curing agent, 0.7 parts of alkali-free glass fiber, 0.4 parts of microcrystalline paraffin, 1.5 parts of montmorillonite, 2 parts of manganese slag, 8 parts of corundum sand, 7 parts of iron ore, and 90 parts of dead burnt magnesia.
Embodiment 2
[0013] Embodiment 2: a molybdenum phenolic resin coated sand material for instrument casting, including the following raw materials in parts by weight: 1 part of molybdenum phenolic resin, 0.02 part of coupling agent, 0.2 part of urotropine, 0.2 part of curing agent, 0.5 parts of alkali-free glass fiber, 0.2 parts of microcrystalline paraffin, 1 part of montmorillonite, 1 part of manganese slag, 5 parts of corundum sand, 5 parts of iron ore, and 85 parts of dead burnt magnesia.
Embodiment 3
[0014] Embodiment 3: a molybdenum phenolic resin coated sand material for instrument casting, including the following raw materials in parts by weight: 2 parts of molybdenum phenolic resin, 0.06 part of coupling agent, 0.5 part of urotropine, 0.5 part of curing agent, 1 part of alkali-free glass fiber, 0.5 part of microcrystalline paraffin, 2 parts of montmorillonite, 3 parts of manganese slag, 10 parts of corundum sand, 10 parts of iron ore, 95 parts of dead burnt magnesia.
PUM
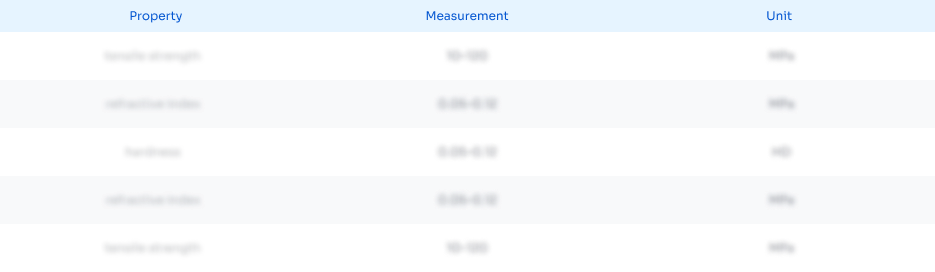
Abstract
Description
Claims
Application Information

- R&D
- Intellectual Property
- Life Sciences
- Materials
- Tech Scout
- Unparalleled Data Quality
- Higher Quality Content
- 60% Fewer Hallucinations
Browse by: Latest US Patents, China's latest patents, Technical Efficacy Thesaurus, Application Domain, Technology Topic, Popular Technical Reports.
© 2025 PatSnap. All rights reserved.Legal|Privacy policy|Modern Slavery Act Transparency Statement|Sitemap|About US| Contact US: help@patsnap.com