Method for preparing cracking-resistant low-shrinking cement mortar with modified coconut fibers
A technology of coir fiber and cement mortar, applied in the direction of climate sustainability, sustainable waste treatment, solid waste management, etc., can solve the problems of large shrinkage deformation, easy cracking, etc. The effect of a small shrinkage value
- Summary
- Abstract
- Description
- Claims
- Application Information
AI Technical Summary
Problems solved by technology
Method used
Image
Examples
Embodiment 1
[0026] The present invention utilizes coconut shell fiber to prepare the method for anti-cracking low-shrinkage cement mortar, and this preparation method comprises the following steps:
[0027] a. Processing of coconut shell fiber:
[0028] First, clean the coconut shell fiber, then dry it (dry in an oven, the drying temperature is 60°C, and the drying time is 2 hours), and cut it into 8-12mm coconut shell fiber after drying;
[0029] b. Preparation of cement mortar:
[0030] 1m 3 Cement mortar is prepared from 720kg of raw cement, 1080kg of sand and 360kg of water; 1m 3 The addition amount of coconut shell fiber in the cement mortar is 0.6kg;
[0031] c. Preparation of anti-cracking low-shrinkage cement mortar:
[0032] 1. first take cement, sand and water according to the proportioning ratio of step b cement mortar, and take coconut shell fiber according to the add-on of coconut shell fiber in cement mortar in addition;
[0033] ② Soak the weighed coconut shell fiber i...
Embodiment 2
[0036] The present invention utilizes coconut shell fiber to prepare the method for anti-cracking low-shrinkage cement mortar, and this preparation method comprises the following steps:
[0037] a. Processing of coconut shell fiber:
[0038] First, clean the coconut shell fiber, then dry it (dry in an oven, the drying temperature is 60°C, and the drying time is 2.5 hours), and cut it into 8-12mm coconut shell fiber after drying;
[0039] b. Preparation of cement mortar:
[0040] 1m 3 Cement mortar is prepared from 720kg of raw cement, 1080kg of sand and 360kg of water; 1m 3 The addition of coconut shell fiber in the cement mortar is 0.8kg;
[0041] c. Preparation of anti-cracking low-shrinkage cement mortar:
[0042] 1. first take cement, sand and water according to the proportioning ratio of step b cement mortar, and take coconut shell fiber according to the add-on of coconut shell fiber in cement mortar in addition;
[0043] ② Soak the weighed coconut shell fiber in wat...
Embodiment 3
[0046] The present invention utilizes coconut shell fiber to prepare the method for anti-cracking low-shrinkage cement mortar, and this preparation method comprises the following steps:
[0047] a. Processing of coconut shell fiber:
[0048] First, clean the coconut shell fiber, then dry it (dry in an oven, the drying temperature is 60°C, and the drying time is 2 hours), and cut it into 8-12mm coconut shell fiber after drying;
[0049] b. Preparation of cement mortar:
[0050] 1m 3 Cement mortar is prepared from 720kg of raw cement, 1080kg of sand and 360kg of water; 1m 3 The addition amount of coconut shell fiber in the cement mortar is 1.0kg;
[0051] c. Preparation of anti-cracking low-shrinkage cement mortar:
[0052] 1. first take cement, sand and water according to the proportioning ratio of step b cement mortar, and take coconut shell fiber according to the add-on of coconut shell fiber in cement mortar in addition;
[0053] ② Soak the weighed coconut shell fiber in ...
PUM
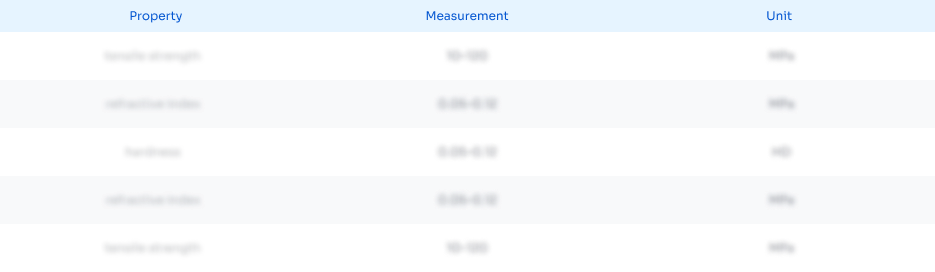
Abstract
Description
Claims
Application Information

- Generate Ideas
- Intellectual Property
- Life Sciences
- Materials
- Tech Scout
- Unparalleled Data Quality
- Higher Quality Content
- 60% Fewer Hallucinations
Browse by: Latest US Patents, China's latest patents, Technical Efficacy Thesaurus, Application Domain, Technology Topic, Popular Technical Reports.
© 2025 PatSnap. All rights reserved.Legal|Privacy policy|Modern Slavery Act Transparency Statement|Sitemap|About US| Contact US: help@patsnap.com