Universal center-adjustment loading mechanism for upper disc
A loading mechanism and centering technology, which is applied in the directions of grinding machine tools, metal processing equipment, grinding devices, etc., can solve problems such as changes in processing efficiency, inability to guarantee the coincidence and parallelism of the two working surfaces, and impact, and achieves the flatness guarantee. Effect
- Summary
- Abstract
- Description
- Claims
- Application Information
AI Technical Summary
Problems solved by technology
Method used
Image
Examples
Embodiment Construction
[0019] The present invention will be described in detail below with reference to the accompanying drawings and in combination with embodiments.
[0020] refer to figure 1 and figure 2 As shown, a universal self-aligning loading mechanism on the upper plate includes a master cylinder 1, the piston rod of the master cylinder 1 is respectively connected to the sensor 5 and the connecting shaft 3, and the connecting shaft 3 is connected to a joint 4 on the universal cross shaft. connected, the universal cross shaft upper joint 4 is provided with a universal joint 6 and a universal cross shaft lower joint 7, and the universal cross shaft upper joint 4 and the universal cross shaft lower joint 7 are respectively on the universal joint 6 The upper and lower ends are fixed and positioned, and the upper joint 4 of the universal cross shaft, the lower joint 7 of the universal cross shaft and the outside of the universal joint 6 are covered with a mandrel 8, and the upper and lower sid...
PUM
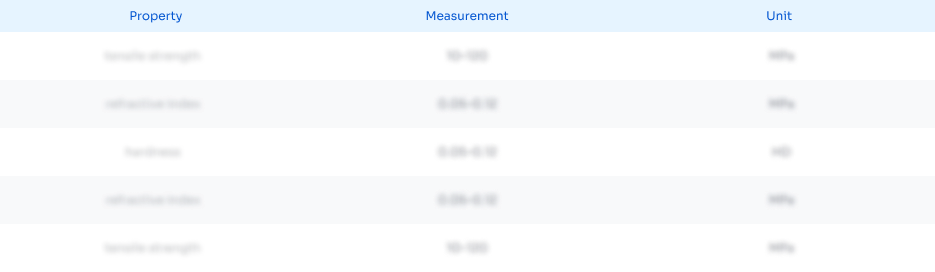
Abstract
Description
Claims
Application Information

- Generate Ideas
- Intellectual Property
- Life Sciences
- Materials
- Tech Scout
- Unparalleled Data Quality
- Higher Quality Content
- 60% Fewer Hallucinations
Browse by: Latest US Patents, China's latest patents, Technical Efficacy Thesaurus, Application Domain, Technology Topic, Popular Technical Reports.
© 2025 PatSnap. All rights reserved.Legal|Privacy policy|Modern Slavery Act Transparency Statement|Sitemap|About US| Contact US: help@patsnap.com