Alkali-resistant rubber hose
A technology of alkali-resistant hose and chlorinated butyl rubber, which is applied in the field of rubber parts manufacturing, can solve the problem that the alkali-resistant performance cannot meet the needs of the industry, and achieve the effect of improving the alkali-resistant performance.
- Summary
- Abstract
- Description
- Claims
- Application Information
AI Technical Summary
Problems solved by technology
Method used
Examples
Embodiment 1
[0011] The alkali-resistant rubber hose of this embodiment is made of the following raw materials:
[0012] Chlorinated butyl rubber 1000g, rosin 60g, petroleum resin 60g, iron oxide 100g, nano-scale perlite powder 1.5g, dilauryl thiodipropionate 200g, zinc stearate 180g, sulfur 2g, isopropanol 10g, Paraffin wax 200g and thiourea dioxide 40g.
[0013] In this example, the above-mentioned raw materials are prepared according to the conventional rubber preparation method. The rubber hose prepared by soaking in a sodium hydroxide solution with a mass concentration of 20% has a weight change rate of 0.25% and a volume change rate of 0.25% after soaking at room temperature for 72 hours. 0.55%.
Embodiment 2
[0015] The alkali-resistant rubber hose of this embodiment is made of the following raw materials:
[0016] Chlorinated butyl rubber 1000g, rosin 100g, petroleum resin 80g, iron oxide 60g, nano-scale perlite powder 1g, dilauryl thiodipropionate 250g, zinc stearate 150g, sulfur 1.5g, isopropanol 30g, 150g of paraffin and 10g of thiourea dioxide.
[0017] In this example, the above-mentioned raw materials are prepared according to the conventional rubber preparation method, and the rubber hose prepared by soaking in a sodium hydroxide solution with a mass concentration of 20% has a weight change rate of 0.28% after soaking at room temperature for 72 hours, and a volume change rate of was 0.56%.
Embodiment 3
[0019] The alkali-resistant rubber hose of this embodiment is made of the following raw materials:
[0020] Chlorobutyl rubber 1000g, rosin 80g, petroleum resin 100g, iron oxide 70g, nano-scale perlite powder 2g, dilauryl thiodipropionate 230g, zinc stearate 200g, sulfur 1g, isopropanol 20g, paraffin wax 180g and thiourea dioxide 50g.
[0021] In this example, the above-mentioned raw materials are prepared according to the conventional rubber preparation method, and the rubber hose prepared by soaking in a sodium hydroxide solution with a mass concentration of 20% has a weight change rate of 0.24% after soaking at room temperature for 72 hours, and a volume change rate of was 0.52%.
PUM
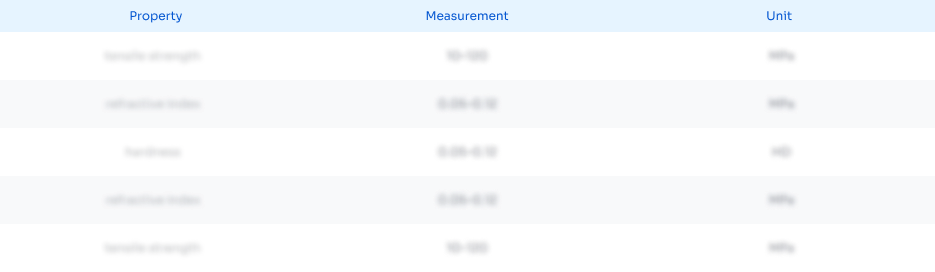
Abstract
Description
Claims
Application Information

- R&D Engineer
- R&D Manager
- IP Professional
- Industry Leading Data Capabilities
- Powerful AI technology
- Patent DNA Extraction
Browse by: Latest US Patents, China's latest patents, Technical Efficacy Thesaurus, Application Domain, Technology Topic, Popular Technical Reports.
© 2024 PatSnap. All rights reserved.Legal|Privacy policy|Modern Slavery Act Transparency Statement|Sitemap|About US| Contact US: help@patsnap.com