Background wall brick preparing method and background wall preparing method
A technology for background walls and green bricks, applied in the field of background wall preparation and background wall brick preparation, can solve the problems that the finished product is prone to produce similar "water ripples", affect the overall aesthetics of the background space, and the production process is complicated, and achieves the development of Small color, flexible formula, good melting performance
- Summary
- Abstract
- Description
- Claims
- Application Information
AI Technical Summary
Problems solved by technology
Method used
Image
Examples
preparation example Construction
[0060] A method for preparing background wall tiles, comprising the following steps:
[0061] 1) forming the green body, drying the green body to obtain a dried green body;
[0062] 2) applying a primer to the surface of the dry body to obtain the first green brick;
[0063] 3) Ink-jet printing on the bottom glaze of the first brick to obtain the second brick;
[0064] 4) drying the second brick to obtain the third brick;
[0065] 5) Apply top glaze to the side of the third brick provided with inkjet printing to obtain the fourth brick;
[0066] 6) drying the fourth brick to obtain the fifth brick;
[0067] 7) Calcining the fifth brick at high temperature to obtain the sixth brick;
[0068] 8) After polishing the sixth adobe brick, edging and waxing are performed in sequence to obtain background wall bricks.
[0069] According to the above operation steps, the background wall tiles of Examples 1-5 were obtained, and relevant components were modified to obtain the backgrou...
Embodiment 1
[0077] A method for preparing background wall tiles, comprising the following steps:
[0078] 1) forming the green body, drying the green body at 105°C for 90 minutes to obtain a dried green body;
[0079] 2) Apply an underglaze to the surface of the dry body to obtain the first green brick; the flow rate of the underglaze is 4.77g / s, the specific gravity is 1.89g / ml, and the application amount of the underglaze is 590g / m 2 , the fineness is 0.3% by weight of dry material after passing through a 325 mesh sieve;
[0080] 3) Ink-jet printing on the bottom glaze of the first brick to obtain the second brick; during ink-jet printing, the parameters of the ink-jet machine are: the belt speed of the ink-jet machine is 20m / min, and the printing size is 910×910mm; The preset pattern is divided and printed on the 12 first bricks (when the 12 first bricks are paved together, a background wall with a complete pattern can be obtained), and the adjacent first bricks are at the joint Set ...
Embodiment 2
[0088] A method for preparing background wall tiles, comprising the following steps:
[0089] 1) forming the green body, drying the green body at 150°C for 90 minutes to obtain a dried green body;
[0090] 2) Apply an underglaze to the surface of the dry body to obtain the first green brick; the flow rate of the underglaze is 4.77g / s, the specific gravity is 1.89g / ml, and the application amount of the underglaze is 590g / m 2 , the fineness is 0.4% by weight of dry material after passing through a 325 mesh sieve;
[0091] 3) Ink-jet printing on the bottom glaze of the first brick to obtain the second brick; during ink-jet printing, the parameters of the ink-jet machine are: the belt speed of the ink-jet machine is 20m / min, and the printing size is 910×910mm; The preset pattern is divided and printed on the 12 first bricks (when the 12 first bricks are paved together, a background wall with a complete pattern can be obtained), and the adjacent first bricks are at the joint Set ...
PUM
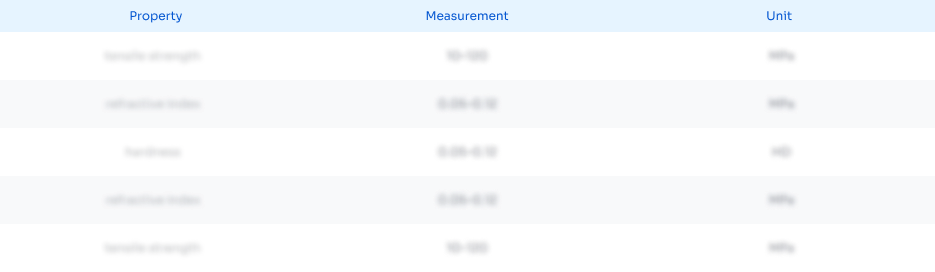
Abstract
Description
Claims
Application Information

- R&D
- Intellectual Property
- Life Sciences
- Materials
- Tech Scout
- Unparalleled Data Quality
- Higher Quality Content
- 60% Fewer Hallucinations
Browse by: Latest US Patents, China's latest patents, Technical Efficacy Thesaurus, Application Domain, Technology Topic, Popular Technical Reports.
© 2025 PatSnap. All rights reserved.Legal|Privacy policy|Modern Slavery Act Transparency Statement|Sitemap|About US| Contact US: help@patsnap.com