SLS scanning method and 3D printing method
A scanning method and 3D printing technology, applied in the direction of additive processing, etc., can solve the problems of difficult dispersion of stress, easy occurrence of stress accumulation, uneven heating of parts, etc., and achieve the effect of stable temperature field, reduced production time, and reduced warping deformation
- Summary
- Abstract
- Description
- Claims
- Application Information
AI Technical Summary
Problems solved by technology
Method used
Image
Examples
example
[0057] For the processing of small batches of electrical connection joints, EOS P110 nylon powder sintering equipment is used, and the supporting software is Magics17.1 and PSW3.6.
[0058] and Figure 6 Traditional print position distributions are shown in different forms, such as Figure 4 and Figure 5 Shown is an example where the printing positions of joint parts are distributed according to the spiral line and sintered. Compared with the traditional printing position distribution, the dimensional accuracy of the parts is changed from ±0.08mm to ±0.05mm, and the defective rate of molded parts is reduced. At the same time, due to the more Optimized preheating temperature, part processing and molding time changed from 10H to 8.5H.
[0059] It can be seen that processing the same parts in the same equipment and adopting a better process can optimize the quality of the product and the processing process to a greater extent within the feasible range.
PUM
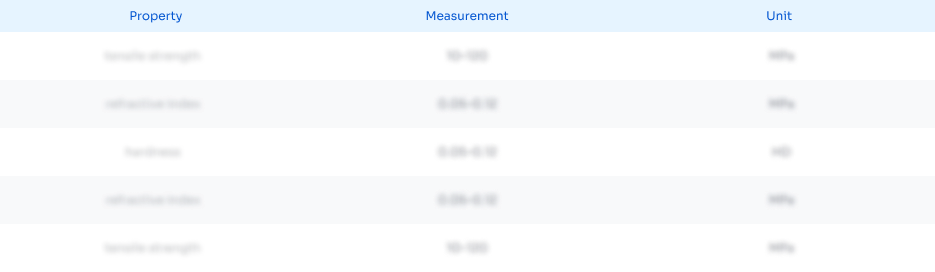
Abstract
Description
Claims
Application Information

- Generate Ideas
- Intellectual Property
- Life Sciences
- Materials
- Tech Scout
- Unparalleled Data Quality
- Higher Quality Content
- 60% Fewer Hallucinations
Browse by: Latest US Patents, China's latest patents, Technical Efficacy Thesaurus, Application Domain, Technology Topic, Popular Technical Reports.
© 2025 PatSnap. All rights reserved.Legal|Privacy policy|Modern Slavery Act Transparency Statement|Sitemap|About US| Contact US: help@patsnap.com