Preparation method of three-dimensional nitrogen-doped carbon fibers
A nitrogen-doped carbon fiber, acidified carbon fiber technology, applied in the direction of carbon fiber, fiber processing, fiber chemical characteristics, etc., can solve the problems of the internal material being unable to contact the electrolyte, small effective specific surface area, and few active sites, etc., to achieve nitrogen doping The effect of high volume, good structural stability and simple operation
- Summary
- Abstract
- Description
- Claims
- Application Information
AI Technical Summary
Problems solved by technology
Method used
Image
Examples
Embodiment 1
[0017] (1) Add 1 g of commercially available chopped carbon fibers into a mixed solution of 30 mL of commercially available concentrated sulfuric acid and 10 mL of commercially available concentrated nitric acid, and react at 60 °C for 2 hours to obtain acidified carbon fibers.
[0018] (2) Put 1 g of the acidified carbon fiber obtained in step (1) into a crucible, and conduct microwave treatment in a microwave oven with a power of 600 W and a treatment time of 8 seconds.
[0019] (3) Mix 200 mg of the product from step (2) with NH 4 Cl is mixed, and the product of step (2) is mixed with NH 4 The mass ratio of Cl is 1:3.
[0020] (4) the mixture obtained in step (3) in N 2 Heat treatment under atmosphere, the heat treatment temperature is 700°C, and the heat treatment time is 3 hours to obtain three-dimensional nitrogen-doped carbon fibers.
Embodiment 2
[0022] (1) Add 1 g of commercially available chopped carbon fibers into a mixed solution of 30 mL of commercially available concentrated sulfuric acid and 10 mL of commercially available concentrated nitric acid, and react at 60 °C for 3 hours to obtain acidified carbon fibers.
[0023] (2) Put 1 g of the acidified carbon fiber obtained in step (1) into a crucible, and conduct microwave treatment in a microwave oven with a power of 700 W and a treatment time of 6 seconds.
[0024] (3) Mix 200 mg of the product from step (2) with (NH 4 ) 2 SO 4 Mix, step (2) gain and (NH 4 ) 2 SO 4 The mass ratio is 2:3.
[0025] (4) the mixture obtained in step (3) in N 2 Heat treatment under atmosphere, the heat treatment temperature is 800°C, and the heat treatment time is 2 hours, to obtain three-dimensional nitrogen-doped carbon fibers.
Embodiment 3
[0027] (1) Add 1 g of commercially available chopped carbon fibers into a mixed solution of 30 mL of commercially available concentrated sulfuric acid and 10 mL of commercially available concentrated nitric acid, and react at 60 °C for 4 hours to obtain acidified carbon fibers.
[0028] (2) Put 1 g of the acidified carbon fiber obtained in step (1) into a crucible, and conduct microwave treatment in a microwave oven with a power of 800 W and a treatment time of 12 seconds.
[0029] (3) Mix 200 mg of the product from step (2) with (NH 4 ) 2 SO 4 Mix, step (2) gain and (NH 4 ) 2 SO 4 The mass ratio is 1:1.
[0030] (4) the mixture obtained in step (3) in N 2 Heat treatment under atmosphere, the heat treatment temperature is 900° C., and the heat treatment time is 3 hours to obtain three-dimensional nitrogen-doped carbon fibers.
PUM
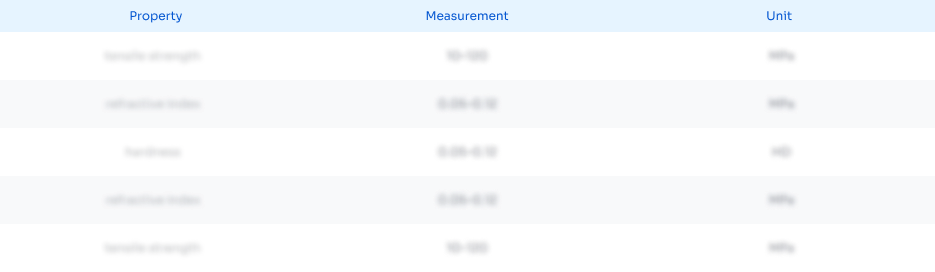
Abstract
Description
Claims
Application Information

- Generate Ideas
- Intellectual Property
- Life Sciences
- Materials
- Tech Scout
- Unparalleled Data Quality
- Higher Quality Content
- 60% Fewer Hallucinations
Browse by: Latest US Patents, China's latest patents, Technical Efficacy Thesaurus, Application Domain, Technology Topic, Popular Technical Reports.
© 2025 PatSnap. All rights reserved.Legal|Privacy policy|Modern Slavery Act Transparency Statement|Sitemap|About US| Contact US: help@patsnap.com