Vertical vibration conveying continuous sintering kiln
A vibrating conveying and sintering kiln technology, applied in the field of powder sintering, can solve the problems of environmental heat radiation, discontinuous production, and high use cost, achieve high temperature uniformity and sealing, high product reactivity, and improve reactivity. Effect
- Summary
- Abstract
- Description
- Claims
- Application Information
AI Technical Summary
Problems solved by technology
Method used
Image
Examples
Embodiment Construction
[0032] The present invention will be described in further detail below in conjunction with the accompanying drawings and specific embodiments.
[0033] Such as Figure 1 to Figure 3 As shown, the vertical vibration conveying continuous sintering kiln of this embodiment includes a furnace body 1, a feed pipe 21, a discharge pipe 22, a feeding device 3 and a heating device 4, and the feeding device 3 includes a column 31, a feeding plate 32. The vibrator 33 and the base assembly 34. The base assembly 34 is located at the bottom of the furnace body 1. The column 31 stands vertically in the furnace body 1 and is installed on the base assembly 34. The feeding plate 32 spirals up around the column 31 to form a spiral feeding Passage 35, vibrator 33 is used for driving column 31 and feeding plate 32 vibrations so that powder moves upwards along spiral feeding passage 35, feed pipe 21 communicates with the bottom end of spiral feeding passage 35, discharge pipe 22 and The top of the ...
PUM
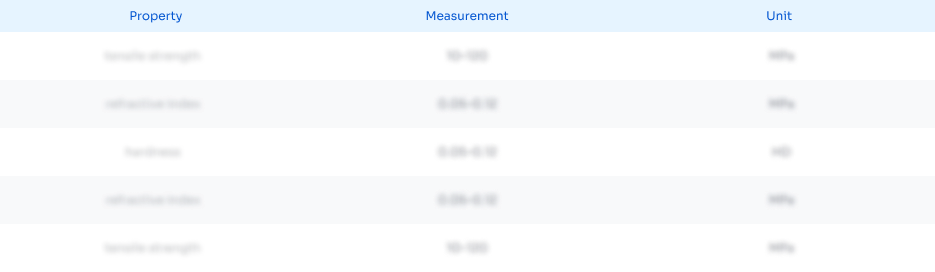
Abstract
Description
Claims
Application Information

- R&D
- Intellectual Property
- Life Sciences
- Materials
- Tech Scout
- Unparalleled Data Quality
- Higher Quality Content
- 60% Fewer Hallucinations
Browse by: Latest US Patents, China's latest patents, Technical Efficacy Thesaurus, Application Domain, Technology Topic, Popular Technical Reports.
© 2025 PatSnap. All rights reserved.Legal|Privacy policy|Modern Slavery Act Transparency Statement|Sitemap|About US| Contact US: help@patsnap.com