Manufacturing process and method of abrasion-resisting lining part
A wear-resistant part and formula technology, which is applied in the production process of wear-resistant lining parts, can solve problems such as poor comprehensive performance, and achieve the effects of good bonding strength, simple production process, improved torque transmission capacity and mechanical strength of friction plates.
- Summary
- Abstract
- Description
- Claims
- Application Information
AI Technical Summary
Problems solved by technology
Method used
Examples
Embodiment Construction
[0028] The disc friction material of the present invention comprises the following raw materials by weight: 10-15 parts of honeycomb zirconia fibers, 15-20 parts of silicon carbide powder, 6-8 parts of adhesive, crystalline zinc borate or 5 parts of crystalline aluminum borate powder -10 parts, the adhesive used includes nitrile modified resin.
[0029] The design idea of the formula of the present invention is to consider that the friction disc should have a higher friction coefficient at high temperature, and the silicon carbide powder, crystal zinc borate, crystal aluminum borate have stable chemical properties at high temperature, and the surface temperature of the automobile brake friction disc can be adjusted Up to 700-800℃, silicon carbide powder, crystalline zinc borate and crystalline aluminum borate can maintain stability at this temperature and provide a stable friction coefficient. Therefore, to improve the heat resistance of the product, it is mainly manifested i...
PUM
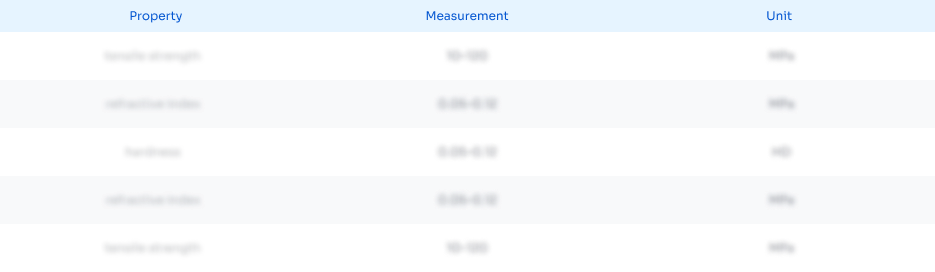
Abstract
Description
Claims
Application Information

- Generate Ideas
- Intellectual Property
- Life Sciences
- Materials
- Tech Scout
- Unparalleled Data Quality
- Higher Quality Content
- 60% Fewer Hallucinations
Browse by: Latest US Patents, China's latest patents, Technical Efficacy Thesaurus, Application Domain, Technology Topic, Popular Technical Reports.
© 2025 PatSnap. All rights reserved.Legal|Privacy policy|Modern Slavery Act Transparency Statement|Sitemap|About US| Contact US: help@patsnap.com