Polystyrene/polypropylene blended heat preservation extruded sheet and preparation method thereof
A technology of polystyrene and polystyrene particles, which is applied in the field of extruded plastic boards, can solve the problems that the flame retardant performance cannot meet the standard and the oxygen index of the board cannot meet the requirements, and achieve the effects of improving the thermal insulation effect, increasing the hardness and increasing the density.
- Summary
- Abstract
- Description
- Claims
- Application Information
AI Technical Summary
Problems solved by technology
Method used
Image
Examples
Embodiment 1
[0027] Embodiment 1: a polystyrene / polypropylene blended thermal insulation extruded board, comprising the following components:
[0028]
[0029]
[0030] Each component is measured in parts by weight, wherein polystyrene particles are composed of polystyrene virgin material and polystyrene recycled material, and the mixing ratio is 3:1, and the carrier of the color masterbatch is polyperfluoroethylene propylene.
[0031] The preparation method of the polystyrene / polypropylene blended insulation extruded board in this embodiment comprises the following steps:
[0032] (1) Re-granulate recycled polystyrene materials, mix them with new polystyrene materials and add them to the mixer, add high-fat-soluble polypropylene, styrene-sodium acrylate, and benzoyl peroxide into the mixer Butyl ester and benzoyl peroxide, start the mixer to mix the materials, and heat the mixed materials to 130°C, keep stirring for 2 hours, then stop and cool;
[0033] (2) Add alkenyl succinate, a...
Embodiment 2
[0035] Embodiment 2: a polystyrene / polypropylene blended insulation extruded board, comprising the following components:
[0036]
[0037]
[0038] Each component is measured in parts by weight, wherein polystyrene particles are composed of polystyrene virgin material and polystyrene recycled material, and the mixing ratio is 3:1, and the carrier of the color masterbatch is polyperfluoroethylene propylene.
[0039] The preparation method of the polystyrene / polypropylene blended insulation extruded board in this embodiment comprises the following steps:
[0040] (1) Re-granulate recycled polystyrene materials, mix them with new polystyrene materials and add them to the mixer, add high-fat-soluble polypropylene, styrene-sodium acrylate, and benzoyl peroxide into the mixer Butyl ester and benzoyl peroxide, start the mixer to mix the materials, and heat the mixed materials to 150°C, keep stirring for 4 hours, then stop and cool;
[0041] (2) Add alkenyl succinate, ammonium ...
Embodiment 3
[0043]Embodiment 3: a polystyrene / polypropylene blended insulation extruded board, including the following components:
[0044]
[0045] Each component is measured in parts by weight, wherein polystyrene particles are composed of polystyrene virgin material and polystyrene recycled material, and the mixing ratio is 3:1, and the carrier of the color masterbatch is polyperfluoroethylene propylene.
[0046] The preparation method of the polystyrene / polypropylene blended insulation extruded board in this embodiment comprises the following steps:
[0047] (1) Re-granulate recycled polystyrene materials, mix them with new polystyrene materials and add them to the mixer, add high-fat-soluble polypropylene, styrene-sodium acrylate, and benzoyl peroxide into the mixer Butyl ester and benzoyl peroxide, start the mixer to mix the materials, and heat the mixed materials to 140°C, keep stirring for 3 hours, then stop and cool;
[0048] (2) Add alkenyl succinate, ammonium benzoate, zinc...
PUM
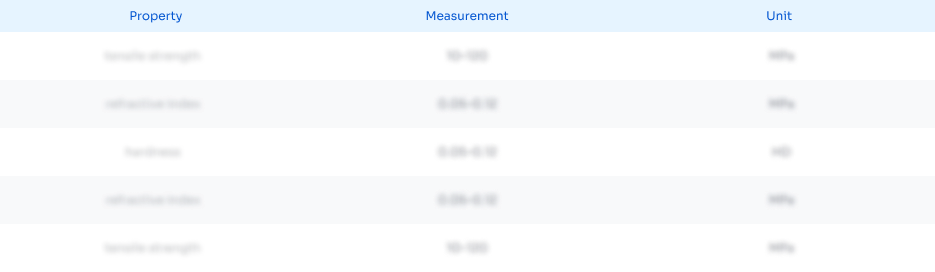
Abstract
Description
Claims
Application Information

- R&D Engineer
- R&D Manager
- IP Professional
- Industry Leading Data Capabilities
- Powerful AI technology
- Patent DNA Extraction
Browse by: Latest US Patents, China's latest patents, Technical Efficacy Thesaurus, Application Domain, Technology Topic, Popular Technical Reports.
© 2024 PatSnap. All rights reserved.Legal|Privacy policy|Modern Slavery Act Transparency Statement|Sitemap|About US| Contact US: help@patsnap.com