Method for preparing hydration-resistant and thermal-shock-resistant calcium oxide crucible by dry process
A calcium oxide crucible and thermal shock resistance technology, applied in the field of oxide refractory materials for high-temperature smelting, can solve the problems of low purity of calcium oxide, easy cracking of calcium oxide crucible, metal or alloy impurities, etc., and achieve good crucible strength and additive distribution. The effect of uniform and lower sintering temperature
- Summary
- Abstract
- Description
- Claims
- Application Information
AI Technical Summary
Problems solved by technology
Method used
Image
Examples
Embodiment 1
[0035] A method for preparing a hydration-resistant, thermal-shock-resistant dry-process calcium oxide crucible, comprising the following steps:
[0036] Step 1, crushing and refining quicklime lumps with a calcium oxide purity greater than 96% to obtain quicklime fines with a particle size of less than 2mm;
[0037] Step 2, uniformly mix the above-mentioned quicklime fines and additives to obtain a 2kg mixture, wherein the quicklime fines account for 91.9% of the total mass percentage of the mixture, and the additives include the following components accounting for the total mass percentage of the mixture, 3% fluorinated Calcium, 3.5% zirconium dioxide, 1% titanium dioxide, 5‰ of boric acid and 1‰ of chromium trioxide; then, the mixture is pressed twice with a press, and the head pressure value of the press for the first time is is 16MPa, the pressure head pressure value of the second press is 12MPa, and the mixture is pressed into brick-shaped products of 2kg each;
[0038]...
Embodiment 2
[0044] A method for preparing a hydration-resistant, thermal-shock-resistant dry-process calcium oxide crucible, comprising the following steps:
[0045] Step 1, crushing and refining quicklime lumps with a calcium oxide purity greater than 96% to obtain quicklime fines with a particle size of less than 2 mm;
[0046] Step 2, uniformly mix the above-mentioned quicklime fines and additives to obtain a 2kg mixture, wherein the quicklime fines account for 91.5% of the total mass percentage of the mixture, and the additives include the following components accounting for the total mass percentage of the mixture, 1% calcium fluoride , 3% zirconium dioxide, 4% titanium dioxide, 2‰ of boric acid and 3‰ of chromium trioxide; 16MPa, the pressure head pressure value of the second press is 19MPa, and the mixture is pressed into brick-shaped products of 2kg each;
[0047] Step 3: Place the brick-shaped products neatly in the temperature-controlled electric furnace, and perform the first ...
Embodiment 3
[0053] A method for preparing a hydration-resistant, thermal-shock-resistant dry-process calcium oxide crucible, comprising the following steps:
[0054] Step 1, crushing and refining quicklime blocks with a calcium oxide purity greater than 98%, to obtain quicklime fines with a particle size of less than 2mm;
[0055] Step 2, uniformly mix the above-mentioned quicklime fines and additives to obtain a 2.25kg mixture, wherein the quicklime fines account for 91.2% of the total mass percentage of the mixture, and the additives include the following components accounting for the total mass percentage of the mixture, 4% fluorine calcium oxide, 4.5% zirconium dioxide, 3‰ of boric acid and 5‰ of chromium trioxide; The head pressure value of the secondary press is 15MPa, and the mixture is pressed into brick-shaped products of 2.25kg each;
[0056] Step 3: Place the brick-shaped products neatly in the temperature-controlled electric furnace, and perform the first temperature-controll...
PUM
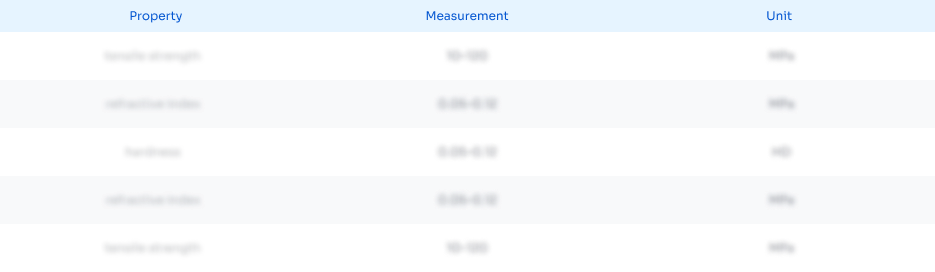
Abstract
Description
Claims
Application Information

- Generate Ideas
- Intellectual Property
- Life Sciences
- Materials
- Tech Scout
- Unparalleled Data Quality
- Higher Quality Content
- 60% Fewer Hallucinations
Browse by: Latest US Patents, China's latest patents, Technical Efficacy Thesaurus, Application Domain, Technology Topic, Popular Technical Reports.
© 2025 PatSnap. All rights reserved.Legal|Privacy policy|Modern Slavery Act Transparency Statement|Sitemap|About US| Contact US: help@patsnap.com