Preparation method of zinc oxide-graphite-like structure carbon nitride flaky nano composite material
A technology of nano-composite material and graphite structure, applied in the field of composite material preparation, can solve the problems of high recombination probability of photogenerated electrons and holes, unable to make full use of solar energy, restricting the practical application of ZnO, etc. Simple preparation process
- Summary
- Abstract
- Description
- Claims
- Application Information
AI Technical Summary
Problems solved by technology
Method used
Image
Examples
Embodiment 1
[0022] Fully mix 3.0g of zinc acetate dihydrate and 7.0g of urea with an agate mortar for 30 minutes, then put the mixed powder into an alumina crucible with a lid, and put it into a muffle furnace for calcination at a temperature of 500 ℃, the heating rate is 10℃ / min, keep warm for 2 hours, then cool down to room temperature naturally, then fully wash with deionized water and absolute ethanol until neutral, and finally dry to prepare zinc oxide-graphite-like structure carbon nitrogen sheet shaped nanocomposites. The prepared zinc oxide-graphite-like structure carbon-nitrogen flake nanocomposite material.
[0023] Such as figure 1 As shown, the prepared ZnO-graphite-like structure carbon-nitrogen flake nanocomposites only show ZnO with hexagonal fibrous crystal structure.
[0024] Such as figure 2 As shown, the prepared ZnO-graphite-like carbon-nitrogen flake nanocomposites show a typical two-dimensional flake structure.
[0025] Such as image 3 As shown, the prepared z...
Embodiment 2
[0029] Fully mix 4.0g of zinc acetate dihydrate and 6.0g of urea with a mixing machine for 30 minutes, then put the mixed powder into an alumina crucible with a lid, put it into a muffle furnace for calcination, and the calcination temperature is 500 ℃, the heating rate is 10°C / min, keep warm for 2 hours, then cool naturally to room temperature, wash thoroughly with deionized water and absolute ethanol in turn until neutral, and finally dry to prepare zinc oxide-graphite-like structure carbon nitrogen flakes nanocomposites. The prepared zinc oxide-graphite-like structure carbon-nitrogen flake nanocomposite material.
Embodiment 3
[0031] Fully mix 2.5g of zinc acetate dihydrate and 7.5g of urea with an agate mortar for 30 minutes, then put the mixed powder into an alumina crucible with a lid, and put it into a muffle furnace for calcination at a temperature of 500 ℃, the heating rate is 10°C / min, keep warm for 2 hours, then cool naturally to room temperature, wash thoroughly with deionized water and absolute ethanol in turn until neutral, and finally dry to prepare zinc oxide-graphite-like structure carbon nitrogen flakes nanocomposites. The prepared zinc oxide-graphite-like structure carbon-nitrogen flake nanocomposite material.
PUM
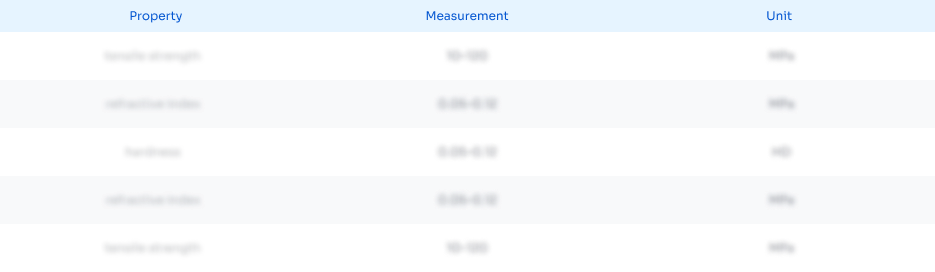
Abstract
Description
Claims
Application Information

- R&D
- Intellectual Property
- Life Sciences
- Materials
- Tech Scout
- Unparalleled Data Quality
- Higher Quality Content
- 60% Fewer Hallucinations
Browse by: Latest US Patents, China's latest patents, Technical Efficacy Thesaurus, Application Domain, Technology Topic, Popular Technical Reports.
© 2025 PatSnap. All rights reserved.Legal|Privacy policy|Modern Slavery Act Transparency Statement|Sitemap|About US| Contact US: help@patsnap.com