High pressure ratio twin spool industrial gas turbine engine
A turbine engine and industrial gas technology, which is applied in the direction of gas turbine devices, engine control, engine components, etc., can solve the problems that the radius of the high rotor shaft cannot be further reduced, the performance of the turbine is not efficient, etc., and achieve the goal of improving thermodynamic efficiency and increasing inlet temperature Effect
- Summary
- Abstract
- Description
- Claims
- Application Information
AI Technical Summary
Problems solved by technology
Method used
Image
Examples
Embodiment Construction
[0035] The present invention is a cooled gas turbine engine with turbine stator vanes. figure 1 A first embodiment of the invention is shown with a gas turbine engine comprising a compressor 11 , a combustion chamber 12 and a turbine 13 , wherein the compressor 11 and turbine 13 are connected together by a rotor shaft. The turbine 13 has a first stage of cooled stator vanes 16 . A compressor 11 compresses air which is then combusted with fuel in a combustor 12 to produce a flow of hot gas which is passed through a turbine 13 . The second compressor 14 is driven by a motor 15 to compress air at a higher pressure than that from the first compressor 11 . The higher compressed air then passes through stator vanes 16 in the turbine 13 for cooling, and the heated cooling gas is then passed into the combustor 12 to combine with fuel and compressed air from the first compressor 11 .
[0036] The second compressor 14 produces high pressure compressed air for cooling of the stator van...
PUM
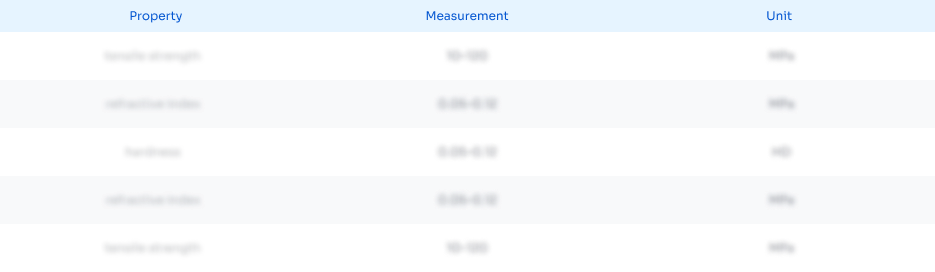
Abstract
Description
Claims
Application Information

- R&D Engineer
- R&D Manager
- IP Professional
- Industry Leading Data Capabilities
- Powerful AI technology
- Patent DNA Extraction
Browse by: Latest US Patents, China's latest patents, Technical Efficacy Thesaurus, Application Domain, Technology Topic, Popular Technical Reports.
© 2024 PatSnap. All rights reserved.Legal|Privacy policy|Modern Slavery Act Transparency Statement|Sitemap|About US| Contact US: help@patsnap.com