Flexible wearable strain sensor based on fabrics and preparation method thereof
A strain sensor and fabric technology, applied in the field of wearable sensors, can solve the problems of low sensitivity, unable to meet the requirements of wearable strain sensors, etc., and achieve the effects of high sensitivity, good cycle stability and durability, and excellent performance.
- Summary
- Abstract
- Description
- Claims
- Application Information
AI Technical Summary
Problems solved by technology
Method used
Image
Examples
Embodiment 1
[0024] Example 1: Preparation of a flexible wearable strain sensor using plain silk fabric as raw material
[0025] A silk fabric with a plain weave structure (the warp yarn is composed of multiple twisted silk fibers, and the weft yarn is composed of multiple parallel silk fibers) is mixed in an argon-based argon-hydrogen gas (the flow ratio of argon to hydrogen is 10:1). Under atmosphere or nitrogen atmosphere, high-temperature heat treatment at 950 ° C to obtain carbonized fabrics that maintain a plain weave structure (the specific temperature rise program is first raised to 150 ° C at a heating rate of 10 ° C / min and kept for 60 min, and then raised to 150 ° C at a heating rate of 5 ° C / min Keep at 350°C for 180min, then rise to 950°C at a rate of 3°C / min and keep for 90min, then cool down to room temperature naturally), the carbonized fabric obtained under this heating program has higher conductivity (its surface resistance is about 140Ω / □); then cut the carbonized f...
Embodiment 2
[0026] Embodiment 2: Mechanism of strain detection of carbonized plain weave structure silk fabric strain sensor
[0027] First, pre-stretch the carbonized plain silk fabric strain sensor, the yarn in the stretching direction is broken, and the micron silk in the yarn perpendicular to the stretching direction is spread out, see the attached Figure 6 (a). In the strain detection process, the pre-stretched strain sensor is used to pre-stretch the broken yarn in the stretching direction. As the strain is applied, the contact point decreases, resulting in an increase in resistance to detect the strain. For the yarn perpendicular to the stretching direction The spreading of the micron silk in the wire ensures a conductive path under large strains resulting in a large detection strain, see appendix Figure 6 (b-d).
Embodiment 3
[0028] Embodiment 3: Cotton fiber fabric and rayon (modal) fabric high temperature heat treatment procedure and conductivity
[0029] Cotton fiber fabrics and modal fabrics are heated to 900°C or 1050°C at a heating rate of 3°C / min in argon-based argon-hydrogen (argon-hydrogen flow ratio 10:1) mixed atmosphere or nitrogen atmosphere, and then Keeping it for 200 minutes, a carbonized fabric with high conductivity and maintaining the original fabric structure can be obtained. The surface resistance of carbonized cotton fiber fabric is about 80Ω / □ (900°C treatment), and the surface resistance of carbonized modal fabric is about 5.5Ω / □ (900°C treatment) and 1.8Ω / □ (1050°C treatment).
PUM
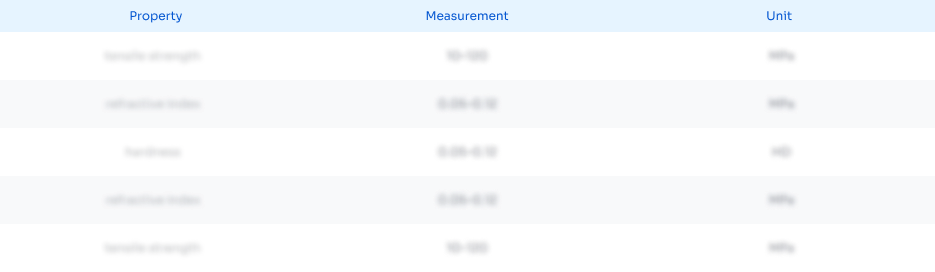
Abstract
Description
Claims
Application Information

- Generate Ideas
- Intellectual Property
- Life Sciences
- Materials
- Tech Scout
- Unparalleled Data Quality
- Higher Quality Content
- 60% Fewer Hallucinations
Browse by: Latest US Patents, China's latest patents, Technical Efficacy Thesaurus, Application Domain, Technology Topic, Popular Technical Reports.
© 2025 PatSnap. All rights reserved.Legal|Privacy policy|Modern Slavery Act Transparency Statement|Sitemap|About US| Contact US: help@patsnap.com