High temperature molten salt method for preparing material with microscopic layered crystal structure
A layered crystal structure, high-temperature melting technology, applied in the direction of molybdenum sulfide, nitrogen and non-metallic compounds, etc., can solve the problems of layered materials such as instability, easy agglomeration, and affecting the application performance of layered nanomaterials, and achieve uniform morphology , not easy to reunite, excellent performance
- Summary
- Abstract
- Description
- Claims
- Application Information
AI Technical Summary
Problems solved by technology
Method used
Image
Examples
Embodiment 1
[0032] Weigh 500 g of LiCl, NaCl, KCl (molar ratio 47.5:15:37.5) and mix them evenly, put them into a quartz crucible, raise the temperature at 5°C / min to 200°C and keep it for 36 hours to remove the moisture in the salt, then raise the temperature at 5°C / min To 550 ℃, keep warm for half an hour to completely melt the salt and form a uniform mixed salt. Weigh 2g of melamine powder, press it into a tablet with a tablet machine, wrap it with nickel foam and tie it to a molybdenum wire, put it in a high-temperature molten salt and react for 40min, and the reaction is carried out under an inert atmosphere of Ar. The nickel foam was taken out and soaked in deionized water for 24 hours, the nickel foam was peeled off, and the product was collected. The obtained product was centrifuged and washed with deionized water and ethanol three times each at a rotational speed of 6000 r / min for 3 minutes. Then the product was dried at 70°C to obtain a layered material of molten salt carbonize...
Embodiment 2
[0036] Weigh Li 2 CO 3 , Na 2 CO 3 , K 2 CO 3 (The molar ratio is 43.5:31.5:25) A total of 500g is mixed evenly and placed in a quartz crucible, heated at 10°C / min to 250°C and kept for 24 hours to remove moisture in the salt, then heated at 10°C / min to 600°C and kept for half an hour until the salt is completely melted and a uniform salt mixture is formed. Weigh 1g ammonium tetrathiomolybdate ((NH 4 ) 2 MoS 4 ) powder, made into tablets with a tablet machine, wrapped with nickel foam and put into high-temperature molten salt to react for 30min, and reacted in N 2 in progress. Take out the foamed copper and soak it in deionized water for 24 hours, then peel off the foamed copper and collect the product. The obtained product was centrifuged and washed with deionized water and ethanol three times each at a rotational speed of 6000 r / min for 3 minutes. Then the product was dried at 80° C. to obtain a layered material of molten salt molybdenum disulfide.
Embodiment 3
[0040]Weigh 500 g of LiCl, NaCl, KCl (molar ratio 47.5:15:37.5) and mix them evenly, put them into a quartz crucible, dry at 200°C for 24 hours to remove the moisture in the salt, raise the temperature to 500°C, and keep it warm until the salt is completely melt. Take by weighing 2g melamine powder and 50mg ammonium tetrathiomolybdate ((NH 4 ) 2 MoS 4 ) powder and mixed evenly, pressed into tablets with a tablet machine, wrapped with nickel foam and put into high-temperature molten salt to react for 30min, and reacted in N 2 in progress. The nickel foam was taken out and soaked in deionized water for 48 hours, then the nickel foam was peeled off and the product was collected. The obtained product was centrifuged and washed with deionized water and ethanol three times each, at a rotational speed of 7000 r / min, for 3 minutes. Then the product is dried at 80° C. to obtain molten salt carbide nitrogen / molybdenum disulfide composite layered material.
PUM
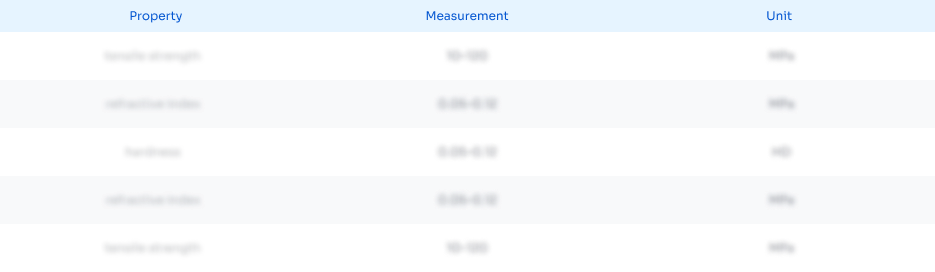
Abstract
Description
Claims
Application Information

- R&D
- Intellectual Property
- Life Sciences
- Materials
- Tech Scout
- Unparalleled Data Quality
- Higher Quality Content
- 60% Fewer Hallucinations
Browse by: Latest US Patents, China's latest patents, Technical Efficacy Thesaurus, Application Domain, Technology Topic, Popular Technical Reports.
© 2025 PatSnap. All rights reserved.Legal|Privacy policy|Modern Slavery Act Transparency Statement|Sitemap|About US| Contact US: help@patsnap.com