Production process of cushion rubber
A production process and cushioning rubber technology, applied in the field of rubber, can solve the problems of easy permanent deformation, high price of natural rubber, large rubber loss factor, etc., and achieve the effect of increasing elasticity, not being prone to permanent deformation, and long service life
- Summary
- Abstract
- Description
- Claims
- Application Information
AI Technical Summary
Problems solved by technology
Method used
Examples
Embodiment 1
[0017] A kind of production technology of buffer rubber, comprises the following steps,
[0018] (1), ingredients: equipped with raw materials, the raw materials include 20 to 30 parts by weight of natural rubber, 16 parts of butadiene rubber, 10 parts of tread reclaimed rubber, 3 parts of toughening agent, 3 parts of elastic agent, silicic acid 0.2 parts of calcium, 1 part of zinc oxide, 0.05 parts of stearic acid, 0.3 parts of plasticizer, 20 parts of anti-aging agent and 10 parts of calcium carbonate; the toughening agent is polyvinyl butyral and dioctyl phthalate, two The addition ratio of the three is 2:1; the elastic agent is butadiene copolymer, ethyl acetate and maleic acid, and the addition ratio of the three is 2:1.5:1;
[0019] (2) Mixing: After fully mixing the raw materials, put them into the mixer for mixing treatment, the mixing temperature is 40°C, and the mixing time is 30 minutes;
[0020] (3) Mold forming: use a mold to shape the kneaded raw materials, and ...
Embodiment 2
[0025] A kind of production technology of buffer rubber, comprises the following steps,
[0026] (1), batching: be equipped with raw material, described raw material comprises 30 parts by weight of natural rubber, 26 parts of butadiene rubber, 20 parts of tread reclaimed rubber, 8 parts of toughening agent, 8 parts of elastic agent, calcium silicate 0.8 part, 1.5 parts of zinc oxide, 0.08 part of stearic acid, 0.5 part of plasticizer, 30 parts of anti-aging agent and 15 parts of calcium carbonate; Described toughening agent is polyvinyl butyral and dioctyl phthalate, The addition ratio of the two is 2:1; the elastic agent is butadiene copolymer, ethyl acetate and maleic acid, and the addition ratio of the three is 2:2:1;
[0027] (2) Mixing: After fully mixing the raw materials, put them into the mixer for mixing treatment, the mixing temperature is 70°C, and the mixing time is 40 minutes;
[0028] (3) Mold forming: use a mold to shape the kneaded raw materials, and then cool...
PUM
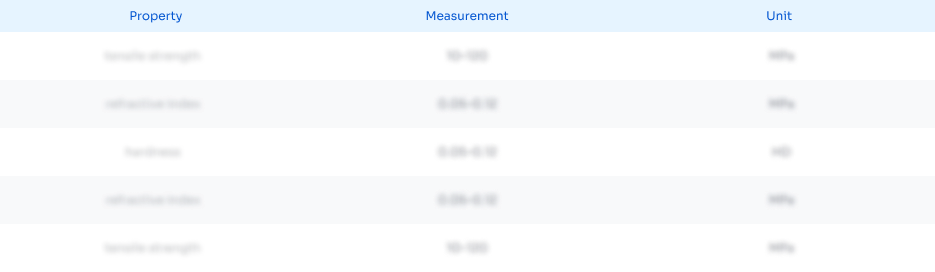
Abstract
Description
Claims
Application Information

- Generate Ideas
- Intellectual Property
- Life Sciences
- Materials
- Tech Scout
- Unparalleled Data Quality
- Higher Quality Content
- 60% Fewer Hallucinations
Browse by: Latest US Patents, China's latest patents, Technical Efficacy Thesaurus, Application Domain, Technology Topic, Popular Technical Reports.
© 2025 PatSnap. All rights reserved.Legal|Privacy policy|Modern Slavery Act Transparency Statement|Sitemap|About US| Contact US: help@patsnap.com