Production method for copper-zinc catalyst
A production method and catalyst technology, which is applied in the production field of copper-zinc catalysts, can solve the problems of catalyst strength fluctuations, difficult one-time molding of roasted particles, etc., and achieve the effect of reducing labor intensity
- Summary
- Abstract
- Description
- Claims
- Application Information
AI Technical Summary
Problems solved by technology
Method used
Image
Examples
Embodiment 1
[0014] First, the ternary slurry is prepared according to the method provided by ZL00133276.7, and then the catalyst production method of the present invention is used to produce the low-pressure methanol catalyst. After adding graphite accounting for 2% of the solid content to the ternary slurry for the production of low-pressure methanol catalyst, mix evenly, the solid content of the ternary slurry is 25%, and form 0.9mm dry particles by spray drying to control the size of the dry particles The water content is 5%, and then the dried particles are formed by tableting with a tablet machine. The filling height of the tablet machine is 30mm, and the height of the tablet is 15mm. The size of the tablet is ?100mm, that is, the compression ratio is 2, and then The tablet is crushed into particles with a diameter of less than 2mm by a pulverizer, the particles are roasted in a far-infrared roaster, and the roasted particles are pressed into a cylindrical tablet of ?5mm×5mm to obtain...
Embodiment 2
[0016] First, the ternary slurry is prepared according to the method provided by ZL00133276.7, and then the catalyst production method of the present invention is used to produce the low-pressure methanol catalyst. After adding graphite accounting for 2% of the solid content to the ternary slurry for the production of low-pressure methanol catalyst, mix evenly, the solid content of the ternary slurry is 25%, and form 0.9mm dry particles by spray drying to control the size of the dry particles The water content is 5%, and then the dry particles are formed by tableting with a tablet machine. The height of the filler in the tablet machine is 30mm, and the height of the tablet is 12mm. The size of the tablet is ?100mm, that is, the compression ratio is 2.5, and then Use a pulverizer to crush the tablet into particles with a diameter less than 2mm, roast the particles in a far-infrared roaster, and press the roasted particles into a cylindrical tablet of ?5mm×5mm to obtain the finis...
Embodiment 3
[0018] The catalyst was prepared according to the method provided in the ZL00133276.7 example as a reference sample. That is, the ternary slurry is washed, filtered and washed, dried, roasted, and shaped to obtain a cylindrical tablet of ?5×5, and the finished product A is obtained. The optimum compression ratio for forming is 3.8.
PUM
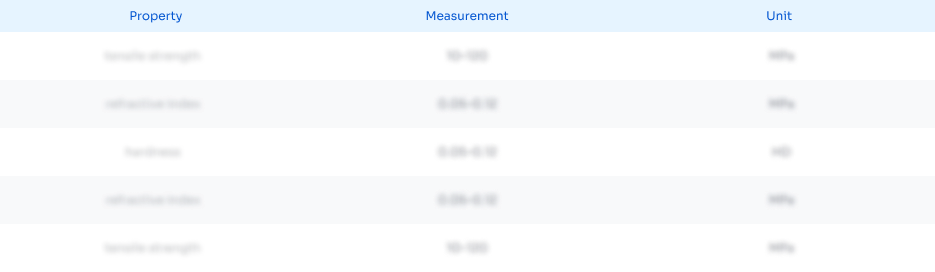
Abstract
Description
Claims
Application Information

- Generate Ideas
- Intellectual Property
- Life Sciences
- Materials
- Tech Scout
- Unparalleled Data Quality
- Higher Quality Content
- 60% Fewer Hallucinations
Browse by: Latest US Patents, China's latest patents, Technical Efficacy Thesaurus, Application Domain, Technology Topic, Popular Technical Reports.
© 2025 PatSnap. All rights reserved.Legal|Privacy policy|Modern Slavery Act Transparency Statement|Sitemap|About US| Contact US: help@patsnap.com