Preparation method of catalytic cracking catalyst
A catalytic cracking and catalyst technology, applied in catalytic cracking, physical/chemical process catalysts, molecular sieve catalysts, etc., can solve the problems of increasing the production cost of oil refining enterprises, the inability to guarantee the strength of the catalyst, and the complex preparation process. The effect of improved cracking capacity and simple preparation process
- Summary
- Abstract
- Description
- Claims
- Application Information
AI Technical Summary
Problems solved by technology
Method used
Image
Examples
Embodiment 1
[0047] a. Catalyst molding: Mix 510g pseudo-boehmite, 2213g kaolin, 278g aluminum sol, 310g USY molecular sieve, 3960g deionized and 51mL hydrochloric acid, homogenize, control the temperature of the tail gas for spray molding to 150°C, and prepare the catalyst. Roasting at 600°C for 30 minutes;
[0048] b. Acid modification: add 4659g of water to the catalyst prepared in step a; add hydrochloric acid to adjust the pH value to 4.5, and stir for 100min;
[0049] c. Modifying agent modification: add ammonium bicarbonate to the catalyst slurry modified in step b to make the pH value equal to 6, and stir for 30min;
[0050] d. Filtration and drying: filter and dry at 90°C;
Embodiment 2
[0053] a. Catalyst molding: Mix 600g pseudo-boehmite, 1770g bentonite, 447g silica sol, 560g REY molecular sieve, 4280g deionized and 40mL hydrochloric acid, homogenize, control the temperature of the tail gas of spray molding to 150°C, and prepare the catalyst. Roasting at 450°C for 45 minutes;
[0054] b. Acid modification: add 1935g water to the catalyst prepared in step a; add hydrochloric acid to adjust the pH value to 3.6, and stir for 60min;
[0055] c. modifier modification: add ammonia water to the catalyst slurry modified in step b to make the pH value equal to 7.8, and stir for 110min;
[0056] d. Filtration and drying: filter and dry at 120°C;
[0057] e. Roasting: Roasting at 450°C for 45 minutes.
Embodiment 3
[0059] a. Catalyst molding: Mix 230g aluminum hydroxychloride, 1960g montmorillonite, 580g aluminum sol, 430g REY, 95gZSM-5 molecular sieve, 4716g deionized, homogeneous, control the temperature of the tail gas for spray molding to 150°C, and prepare the catalyst. Roast at 500°C for 35 minutes;
[0060] b. Acid modification: add 2890g water to the catalyst prepared in step a; add nitric acid to adjust the pH value to 3.0, and stir for 35min;
[0061] c. modifier modification: add ammonium carbonate to the catalyst slurry modified in step b to make the pH value equal to 6.6, and stir for 50 min;
[0062] d. Filtration and drying: filter and dry at 150°C;
[0063] e. Roasting: 350°C for 60 minutes.
PUM
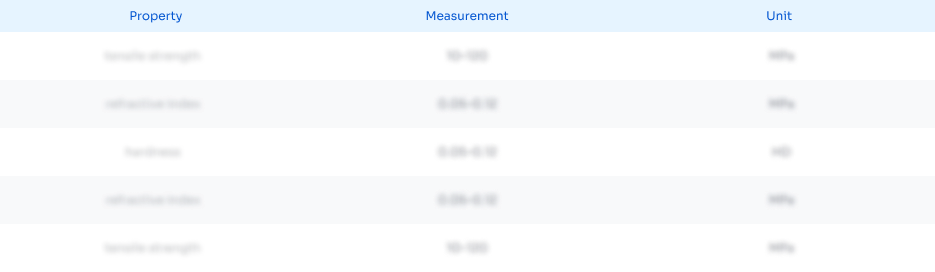
Abstract
Description
Claims
Application Information

- R&D
- Intellectual Property
- Life Sciences
- Materials
- Tech Scout
- Unparalleled Data Quality
- Higher Quality Content
- 60% Fewer Hallucinations
Browse by: Latest US Patents, China's latest patents, Technical Efficacy Thesaurus, Application Domain, Technology Topic, Popular Technical Reports.
© 2025 PatSnap. All rights reserved.Legal|Privacy policy|Modern Slavery Act Transparency Statement|Sitemap|About US| Contact US: help@patsnap.com