Reduction smelting slag and application of reduction smelting slag to reduction smelting of coarse antimony oxide
A technology for smelting slag and antimony oxide, which is applied in the reduction smelting slag and its application in the reduction smelting of crude antimony oxide, can solve the problems of low antimony direct recovery rate, high volatilization powder return, high antimony content in slag, and achieve fluidity Good, less volatilization powder return, low antimony content in slag
- Summary
- Abstract
- Description
- Claims
- Application Information
AI Technical Summary
Problems solved by technology
Method used
Image
Examples
Embodiment 1
[0043] In this embodiment, 100g of crude antimony oxide is used as raw material, and its chemical composition is Sb78.5%, SiO 2 1.41%, Fe0.36%, CaO0.09%, Na0.05%, S1.39%. Combine the crude antimony oxide with 10g coke powder (84.44% carbon content) and an appropriate amount of SiO 2 , FeC 2 o 4 2H 2 O, CaO, Na 2 CO 3 Mixing chemically pure reagents, designing SiO slag 2 , FeO, CaO, Na 2 The mass percentage between O and O is 34:38:12:16, and the amount of slag is 25g. Put the material into a corundum crucible and put it into a resistance furnace at room temperature, raise the temperature to 1000°C at a rate of 10°C / min and keep it warm and static. Place it for 50 minutes, and produce crude antimony and slag after the heat preservation is over, the direct recovery rate of antimony metal is 90.35%, and the slag contains 0.74% antimony. The grade of the obtained crude antimony is 96.61%.
Embodiment 2
[0045] In this embodiment, 100g of crude antimony oxide is used as raw material, and its chemical composition is Sb78.5%, SiO 2 1.41%, Fe0.36%, CaO0.09%, Na0.05%, S1.39%. Combine the crude antimony oxide with 11g coke powder (88.44% carbon content) and an appropriate amount of SiO 2 , FeC 2 o 4 2H 2 O, CaO, Na 2 CO 3 Mixing chemically pure reagents, designing SiO in slag 2 , FeO, CaO, Na 2 The mass percentage between O is 30:34:12:24, and the amount of slag is 28g. Put the material into a corundum crucible and put it into a resistance furnace at room temperature, raise the temperature to 1000°C at a rate of 10°C / min, keep it warm, and let it stand for 50 minutes. After the heat preservation is over, crude antimony and slag will be produced. %, the slag contains 0.97% antimony. The grade of the obtained crude antimony is 98.49%.
Embodiment 3
[0047] In this embodiment, 100g of crude antimony oxide is used as raw material, and its chemical composition is Sb78.5%, SiO 2 1.41%, Fe0.36%, CaO0.09%, Na0.05%, S1.39%. Combine the crude antimony oxide with 12g coke powder (88.44% carbon content) and an appropriate amount of SiO 2 , FeC 2 o 4 2H 2 O, CaO, Na 2 CO 3 Mixing chemically pure reagents, designing SiO slag 2 , FeO, CaO, Na 2 The mass percentage between O is 30:30:12:28, and the amount of slag is 30g. Put the material into a corundum crucible and put it into a resistance furnace at room temperature, raise the temperature to 1000°C at a rate of 10°C / min, keep it warm, and let it stand for 50 minutes. %, the slag contains 0.93% antimony. The grade of the obtained crude antimony is 97.05%.
PUM
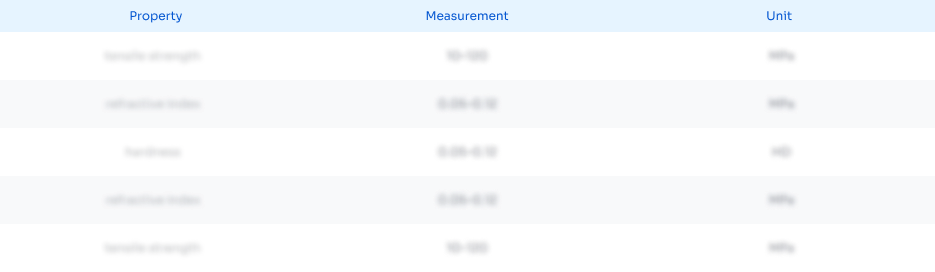
Abstract
Description
Claims
Application Information

- R&D Engineer
- R&D Manager
- IP Professional
- Industry Leading Data Capabilities
- Powerful AI technology
- Patent DNA Extraction
Browse by: Latest US Patents, China's latest patents, Technical Efficacy Thesaurus, Application Domain, Technology Topic, Popular Technical Reports.
© 2024 PatSnap. All rights reserved.Legal|Privacy policy|Modern Slavery Act Transparency Statement|Sitemap|About US| Contact US: help@patsnap.com