Polypyrrolone/polyimide composite porous catalytic film and preparation method thereof
A technology of polyimide and polypyrrole, which is applied in the field of polypyrrole/polyimide composite porous catalytic membrane and its preparation, can solve problems such as limitations in use performance, and achieve cost reduction, multiple active centers, and good mechanical properties. performance effect
- Summary
- Abstract
- Description
- Claims
- Application Information
AI Technical Summary
Problems solved by technology
Method used
Image
Examples
preparation example Construction
[0049] In the preparation of the polypyrrone precursor solution in step (1), exemplary tetraacid monomers include, but are not limited to, 3,3′,5,5′-biphenyltetracarboxylic acid, 3,3′,4, 4'-Biphenyltetracarboxylic acid, 3,3',5,5'-benzophenone tetracarboxylic acid, 3,3',4,4'-benzophenone tetracarboxylic acid, 2,3,3',4'- Diphenyl ether tetracarboxylic acid, 3,3',5,5'-diphenyl ether tetracarboxylic acid, 3,3',4,4'-diphenyl ether tetracarboxylic acid, 3,3',5,5'-diphenyl ether tetracarboxylic acid Methyl methane tetracarboxylic acid, 3,3',4,4'-diphenylmethane tetracarboxylic acid, 2,2',3,3'-diphenylmethane tetracarboxylic acid, 2,2',3,4-diphenyl Methyl methane tetracarboxylic acid, 3,3',4,4'-bistrifluoromethyldiphenyltetracarboxylic acid, 3,3',5,5'-bistrifluoromethyldiphenyltetracarboxylic acid, 2,2 ',3,3'-bistrifluoromethyldiphenyltetracarboxylic acid, 2,2',4,4'-bistrifluoromethyldiphenyltetracarboxylic acid, 2,3,3',4'-bis Trifluoromethyldiphenyltetracarboxylic acid, 1,4,5,8-nap...
Embodiment 1
[0120] Under the condition of lower than 25° C., A1 and B1 monomers with a molar ratio of 1:1 were dissolved in C1, and magnetically stirred for 2 hours to obtain a polypyrrolene precursor solution with a mass concentration of 15%. The polyamic acid solution is mainly prepared from D1 and E1, wherein the molar ratio of D1, E1 to benzoic acid is 1:2:0.5; finally a polyamic acid (PAA) solution with a mass concentration of 20% is obtained. Then the PAA solution is added to the above-mentioned polypyrrolone precursor solution, and then the metal component: F1, pore-forming agent: G1; the polypyrrole precursor solution, the polyamic acid solution, the The mass ratio of the metal component to the pore-forming agent is: 100:50:10:20. Stir for 4 hours to make it evenly mixed to obtain a spinning mixture.
[0121] The spinning mixed solution was subjected to electrospinning, the spinning voltage was controlled at 15kV, and the distance from the spinning nozzle to the opposite electrod...
Embodiment 2
[0123] Under the condition of lower than 25° C., A2 and B2 monomers with a molar ratio of 1:1 were dissolved in C2, and magnetically stirred for 2 hours to obtain a polypyrrolone precursor solution with a mass concentration of 25%. The polyamic acid solution is mainly prepared from D2 and E2, wherein the molar ratio of D2, E2 and benzoic acid is 1:1:0.5; finally a polyamic acid (PAA) solution with a mass concentration of 15% is obtained. Then the PAA solution is added to the above-mentioned polypyrrole precursor solution, and then the metal component: F2, pore-forming agent: G2 are added in sequence; the polypyrrole precursor solution, the polyamic acid solution, the The mass ratio of the metal component to the pore-forming agent is: 100:80:5:10. Stir for 4 hours to make it evenly mixed to obtain a spinning mixture.
[0124] Electrospinning was carried out on the above-mentioned spinning mixed liquid, the spinning voltage was controlled at 40 kV, and the distance from the spi...
PUM
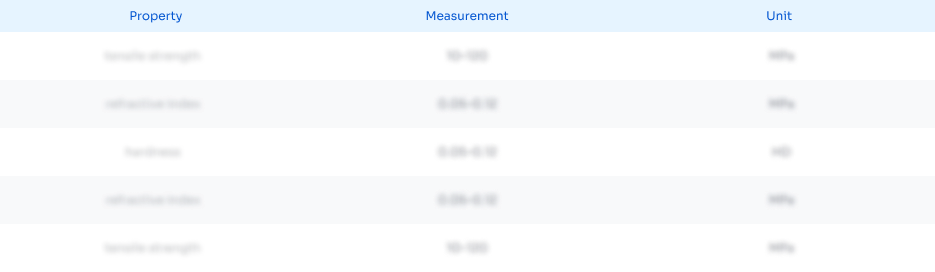
Abstract
Description
Claims
Application Information

- Generate Ideas
- Intellectual Property
- Life Sciences
- Materials
- Tech Scout
- Unparalleled Data Quality
- Higher Quality Content
- 60% Fewer Hallucinations
Browse by: Latest US Patents, China's latest patents, Technical Efficacy Thesaurus, Application Domain, Technology Topic, Popular Technical Reports.
© 2025 PatSnap. All rights reserved.Legal|Privacy policy|Modern Slavery Act Transparency Statement|Sitemap|About US| Contact US: help@patsnap.com