Iron piece chemical nickel plating process
An electroless nickel plating and process technology, applied in the field of electroless nickel plating of iron parts, can solve the problems of low market competitiveness of products, low production efficiency, complexity, etc., to avoid repetitive processes, improve work efficiency, and simple methods Effect
- Summary
- Abstract
- Description
- Claims
- Application Information
AI Technical Summary
Problems solved by technology
Method used
Examples
Embodiment Construction
[0015] The technical solution disclosed by the present invention is an electroless nickel plating process for iron parts, which is characterized in that it includes the following steps: 1) Degreasing: use 5%-10% degreasing powder to heat to 65-70 degrees and soak for 5-10 minute;
[0016] 2) Washing: Rinse the blind holes and dead corners thoroughly in the sink, or with tap water. There should be no degreasing powder residue. If possible, use a soft cloth to wipe the surface with your hands to ensure that the oil is better removed;
[0017] 3) Pickling activation: use 15%-20% hydrochloric acid, and the activation time is 1-3 minutes. The long time is mainly determined by the workpiece. If the workpiece itself has too much rust, please remove it before degreasing. rust;
[0018] 4) Water washing: use a sink or tap water to rinse thoroughly, so as not to bring residual hydrochloric acid into the aqueduct, and the dead corners of blind holes must be rinsed with a water gun;
[...
PUM
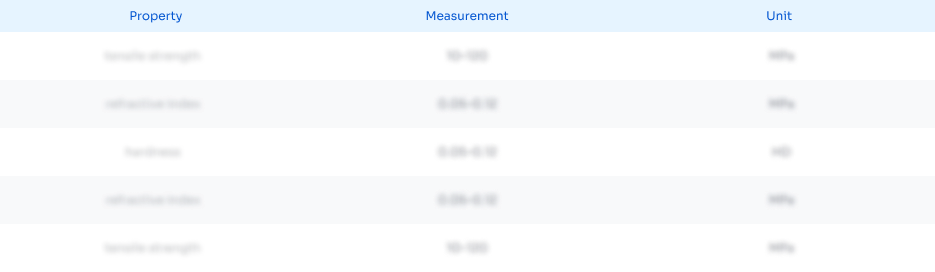
Abstract
Description
Claims
Application Information

- R&D Engineer
- R&D Manager
- IP Professional
- Industry Leading Data Capabilities
- Powerful AI technology
- Patent DNA Extraction
Browse by: Latest US Patents, China's latest patents, Technical Efficacy Thesaurus, Application Domain, Technology Topic, Popular Technical Reports.
© 2024 PatSnap. All rights reserved.Legal|Privacy policy|Modern Slavery Act Transparency Statement|Sitemap|About US| Contact US: help@patsnap.com