Method for extracting vanadium from ammonium phosphate leaching vanadium containing raw clinker
An ammonium phosphate and raw material technology, applied in the field of vanadium chemical metallurgy, can solve the problems of ammonium salt loss, short technological process, low production cost, etc., and achieve the effects of avoiding ammonia volatilization, friendly operation environment and low production cost
- Summary
- Abstract
- Description
- Claims
- Application Information
AI Technical Summary
Problems solved by technology
Method used
Examples
Embodiment 1
[0033] will V 2 o 5 Vanadium slag with a content of 11% was roasted at 700°C for 2 hours. The clinker was leached to extract vanadium in a solution with an ammonium phosphate concentration of 200g / L. The leaching temperature was 40°C, the leaching liquid-solid ratio was 20mL / g, and the leaching time was After 5h, the leaching residue and vanadium-containing liquid were obtained after filtration.
[0034] The leached slag was washed, dried, weighed and analyzed for the vanadium content of the residue. It was tested that the vanadium transfer leaching rate was 95%.
Embodiment 2
[0036] will V 2 o 5 Vanadium slag with a content of 15% was roasted at 950°C for 0.5h. The clinker was leached to extract vanadium in a solution with an ammonium phosphate concentration of 500g / L. The leaching temperature was 70°C, the leaching liquid-solid ratio was 5mL / g, and the leaching time was After 1h, the leaching residue and vanadium-containing liquid were obtained after filtration.
[0037] The leached slag was washed, dried, weighed and analyzed for the vanadium content of the residue. It was tested that the vanadium transfer leaching rate was 91%.
Embodiment 3
[0039] will V 2 o 5 Vanadium slag with a content of 20% was roasted at 850°C for 1 hour. The clinker was leached to extract vanadium in a solution with an ammonium phosphate concentration of 600g / L. The leaching temperature was 90°C, the leaching liquid-solid ratio was 10mL / g, and the leaching time was After 1h, the leaching residue and vanadium-containing liquid were obtained after filtration.
[0040] The leached slag was washed, dried, weighed and analyzed for the vanadium content of the residue, and the vanadium transfer leaching rate was detected to be 94%.
PUM
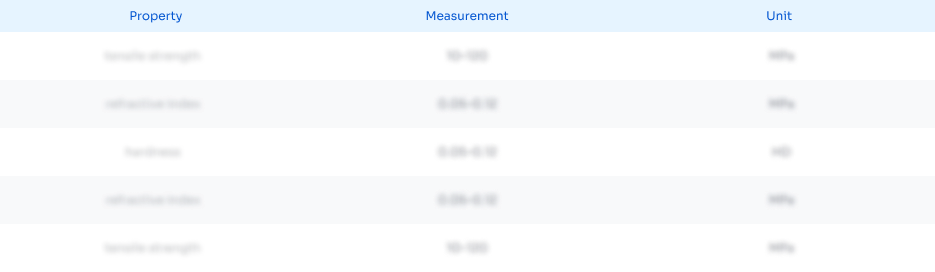
Abstract
Description
Claims
Application Information

- R&D
- Intellectual Property
- Life Sciences
- Materials
- Tech Scout
- Unparalleled Data Quality
- Higher Quality Content
- 60% Fewer Hallucinations
Browse by: Latest US Patents, China's latest patents, Technical Efficacy Thesaurus, Application Domain, Technology Topic, Popular Technical Reports.
© 2025 PatSnap. All rights reserved.Legal|Privacy policy|Modern Slavery Act Transparency Statement|Sitemap|About US| Contact US: help@patsnap.com