Method for separating ethylbenzene dehydrogenation reaction products
A technology for reaction products and separation methods, applied in distillation purification/separation, organic chemistry, etc., can solve the problems of high energy consumption of separation devices and large loss of styrene polymerization, and achieve reduced polymerization loss, reduced separation energy consumption, and good technology. effect of effect
- Summary
- Abstract
- Description
- Claims
- Application Information
AI Technical Summary
Problems solved by technology
Method used
Image
Examples
Embodiment 1
[0018] A 100,000 tons / year styrene plant (annual operating hours 8000 hours), its styrene separation system adopts figure 1 The process, the ethylbenzene / styrene separation tower feed flow rate is 21.5 tons / hour, the weight percentage is composed of: benzene 0.4%, toluene 1.4%, ethylbenzene 36%, styrene 60%, heavy component 2.2%, the main operating conditions And consumption see Table 1:
[0019] Table 1
[0020] Ethylbenzene / styrene separation tower T101 top pressure kPaA
[0021] Compressor C101 outlet pressure KPaA
Embodiment 2
[0023] A 100,000 tons / year styrene plant (annual operating hours 8000 hours), its styrene separation system adopts figure 1 The process, the ethylbenzene / styrene separation tower feed flow rate is 22 tons / hour, the weight percentage is composed of: benzene 0.3%, toluene 1.5%, ethylbenzene 38%, styrene 58%, heavy component 2.2%, main operating conditions And consumption see Table 2:
[0024] Table 2
[0025] Ethylbenzene / styrene separation tower T101 top pressure kPaA
Embodiment 3
[0027] A 100,000 tons / year styrene plant (annual operating hours 8000 hours), its styrene separation system adopts figure 1 The process, the ethylbenzene / styrene separation tower feed flow rate is 22 tons / hour, the weight percentage is composed of: benzene 0.3%, toluene 1.5%, ethylbenzene 38%, styrene 58%, heavy component 2.2%, main operating conditions And consumption see Table 3:
[0028] table 3
[0029] Ethylbenzene / styrene separation tower T101 top pressure kPaA
PUM
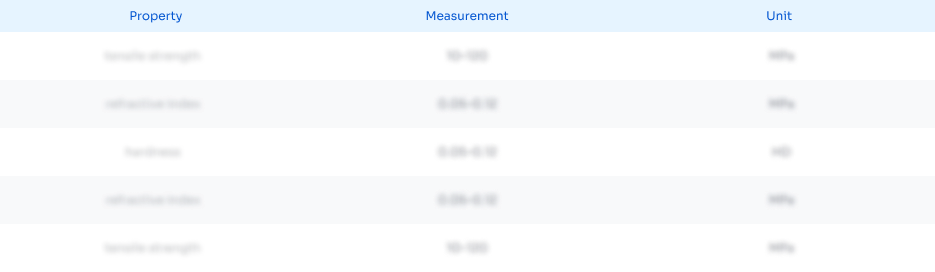
Abstract
Description
Claims
Application Information

- Generate Ideas
- Intellectual Property
- Life Sciences
- Materials
- Tech Scout
- Unparalleled Data Quality
- Higher Quality Content
- 60% Fewer Hallucinations
Browse by: Latest US Patents, China's latest patents, Technical Efficacy Thesaurus, Application Domain, Technology Topic, Popular Technical Reports.
© 2025 PatSnap. All rights reserved.Legal|Privacy policy|Modern Slavery Act Transparency Statement|Sitemap|About US| Contact US: help@patsnap.com