High-recovery quench process of acrylonitrile
A high-recovery, acrylonitrile technology, applied in the purification/separation of carboxylic acid nitrile, organic chemistry and other directions, can solve the problems of uneven spraying, low recovery rate of acrylonitrile, etc., to improve the ammonia removal effect, improve the recovery rate, The effect of reducing polymerization loss
- Summary
- Abstract
- Description
- Claims
- Application Information
AI Technical Summary
Problems solved by technology
Method used
Image
Examples
Embodiment 1
[0024] The reaction gas entering the quenching tower contains 42 grams of acrylonitrile per hour, the temperature is 210°C, the upper section is 5 theoretical plates, and the lower section is an empty tower. , the spray volume of the upper section circulation is 123.6 ml / min, and sulfuric acid is added into the upper section circulating fluid to control the pH value of the upper section circulating fluid to be 3.5. The weight ratio of the spray amount in the lower section to the reaction gas entering the quench tower is 0.4, the temperature of the spray liquid is 82°C, the discharge rate is 0.4 ml / min, and the pH value of the kettle liquid is 7.5. The gas at the outlet of the tower top contains 40.6 g / h of acrylonitrile, and the recovery rate of acrylonitrile in the quenching tower is 96.7%.
Embodiment 2
[0026] The reaction gas entering the quenching tower contains 42 grams of acrylonitrile per hour, the temperature is 210°C, the upper section is 5 theoretical plates, and the lower section is an empty tower. , the spray volume of the upper section circulation is 123.6 ml / min, and sulfuric acid is added into the upper section circulating fluid to control the pH value of the upper section circulating fluid to be 3.5. The weight ratio of the spray volume in the lower stage to the reaction gas entering the quenching tower is 4.0, the blowdown rate is 0.4 ml / min, and oxalic acid is directly added to the tower kettle to adjust the pH value of the kettle liquid to 7.0. The gas at the outlet of the tower top contains 40.0 g / h of acrylonitrile, and the recovery rate of acrylonitrile in the quenching tower is 95.2%.
Embodiment 3
[0028] The reaction gas entering the quenching tower contains 42 grams of acrylonitrile per hour, the temperature is 210°C, the upper section is 5 theoretical plates, and the lower section is an empty tower. , the spray volume of the upper section circulation is 123.6 ml / min, and sulfuric acid is added into the upper section circulating fluid to control the pH value of the upper section circulating fluid to be 3.5. The weight ratio of the lower cycle spraying amount to the reaction gas entering the quenching tower is 2.0, and the weight concentration of acrylonitrile, hydrocyanic acid or acrolein polymers and their mixtures in the tower kettle is 0.5% by increasing the supplementary water amount, and directly added with oxalic acid In the bottom tower kettle, adjust the pH value of the kettle liquid to 7.3. The gas at the outlet of the tower top contains 40.2 g / h of acrylonitrile, and the recovery rate of acrylonitrile in the quenching tower is 95.7%.
PUM
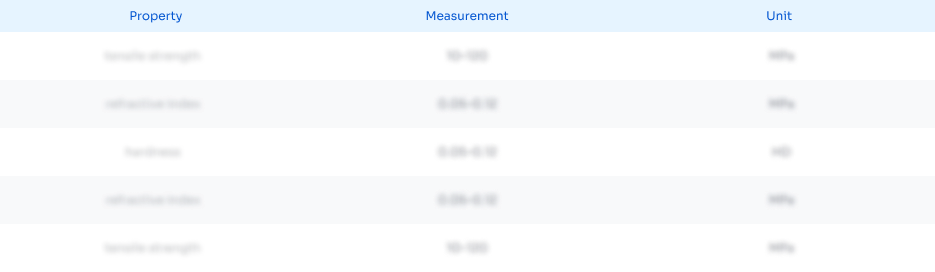
Abstract
Description
Claims
Application Information

- Generate Ideas
- Intellectual Property
- Life Sciences
- Materials
- Tech Scout
- Unparalleled Data Quality
- Higher Quality Content
- 60% Fewer Hallucinations
Browse by: Latest US Patents, China's latest patents, Technical Efficacy Thesaurus, Application Domain, Technology Topic, Popular Technical Reports.
© 2025 PatSnap. All rights reserved.Legal|Privacy policy|Modern Slavery Act Transparency Statement|Sitemap|About US| Contact US: help@patsnap.com