Method for dearsenization of arsenic containing waste water generated in regeneration process of vanadium, tungsten and titanium denitration catalyst
A denitrification catalyst and regeneration process technology, applied in the field of arsenic-containing wastewater, can solve the problems of environmental secondary pollution, catalyst arsenic poisoning, reduce the service life of the catalyst, etc., and achieve the effect of reducing costs and simplifying the process
- Summary
- Abstract
- Description
- Claims
- Application Information
AI Technical Summary
Problems solved by technology
Method used
Image
Examples
Embodiment 1
[0025] Such as figure 1 As shown, firstly, the arsenic-containing vanadium-tungsten-titanium denitrification catalyst sample is subjected to alkali leaching and arsenic removal reaction with sodium hydroxide solution. After the reaction, the catalyst and arsenic-containing wastewater after alkali leaching are obtained; at this time, the As content in the arsenic-containing wastewater is 0.6~1.0g / l; the concentration of sodium hydroxide in the solution containing sodium hydroxide used in the alkali leaching and arsenic removal reaction is 200g / L, the reaction time is 3h, and the reaction temperature is >95°C.
[0026] Adding oxidant hydrogen peroxide (H 2 o 2 ), press H 2 o 2 :As stoichiometric ratio 1:1, control oxidation temperature 100°C, reaction time 0.5h, add iron salt (ferric sulfate) after oxidation reaction to adjust solution pH > 9, at 60°C, add a certain amount of CaO (according to Ca :As molar ratio=1:1), the reaction time is 1h. After the reaction, liquid-soli...
Embodiment 2
[0028] First, the arsenic-containing vanadium-tungsten-titanium denitrification catalyst sample is subjected to alkali leaching de-arsenization reaction with sodium hydroxide solution. After the reaction, the catalyst and arsenic-containing wastewater after alkali leaching are obtained; at this time, the As content in the arsenic-containing wastewater is 0.6-1.0 g / l; the concentration of sodium hydroxide in the solution containing sodium hydroxide used in the alkali leaching reaction for arsenic removal is 200g / L, the reaction time is 5h, and the reaction temperature is >95°C.
[0029] Adding oxidant hydrogen peroxide (H 2 o 2 ), press H 2 o 2 : As stoichiometric ratio 3:1, control oxidation temperature 20°C, reaction time 2h, add iron salt (ferric sulfate) after oxidation reaction to adjust solution pH > 9, at 80°C, add a certain amount of CaO (according to Ca: As molar ratio=1:1), the reaction time is 1h. After the reaction, liquid-solid separation is carried out to obta...
Embodiment 3
[0031] First, the arsenic-containing vanadium-tungsten-titanium denitrification catalyst sample is subjected to alkali leaching de-arsenization reaction with sodium hydroxide solution. After the reaction, the catalyst and arsenic-containing wastewater after alkali leaching are obtained; at this time, the As content in the arsenic-containing wastewater is 0.6-1.0 g / l; the concentration of sodium hydroxide in the solution containing sodium hydroxide used in the alkali leaching and arsenic removal reaction is 150g / L, the reaction time is 4h, and the reaction temperature is >95°C.
[0032] Adding oxidant hydrogen peroxide (H 2 o 2 ), press H 2 o 2 :As stoichiometric ratio 5:1, control oxidation temperature 30°C, reaction time 2h, add iron salt (ferric sulfate) after oxidation reaction to adjust solution pH > 9, at 100°C, add a certain amount of CaO (according to Ca: As molar ratio=2:1), the reaction time is 3h. After the reaction, liquid-solid separation is carried out to obta...
PUM
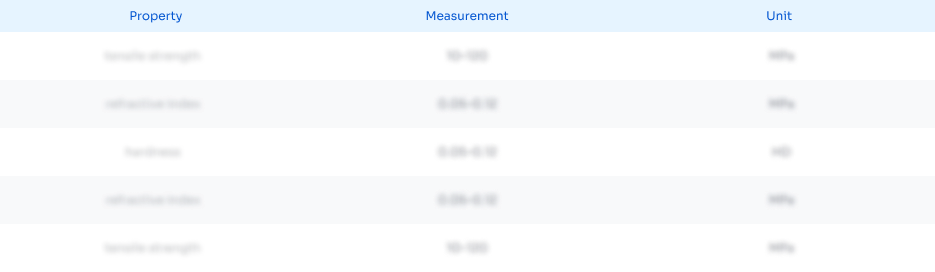
Abstract
Description
Claims
Application Information

- R&D
- Intellectual Property
- Life Sciences
- Materials
- Tech Scout
- Unparalleled Data Quality
- Higher Quality Content
- 60% Fewer Hallucinations
Browse by: Latest US Patents, China's latest patents, Technical Efficacy Thesaurus, Application Domain, Technology Topic, Popular Technical Reports.
© 2025 PatSnap. All rights reserved.Legal|Privacy policy|Modern Slavery Act Transparency Statement|Sitemap|About US| Contact US: help@patsnap.com