Preparation method of water based flow coating for 3D printing sand mold
A 3D printing, sand molding technology, applied in casting molding equipment, coating, mold and other directions, to achieve the effect of no accumulation, superior fluidity, and low sintering temperature
- Summary
- Abstract
- Description
- Claims
- Application Information
AI Technical Summary
Problems solved by technology
Method used
Image
Examples
Embodiment 1
[0035] The production raw materials of a 3D printing sand mold water-based flow coating coating are: zircon powder refractory aggregate 70%, sodium bentonite 3%, sepiolite powder 1%, polyvinyl alcohol 0.5%, phosphate 0.2%, sulfonated amber Dioctyl acid sodium salt 0.1%, DY-preservative 0.2%, fluorite 0.3%, iron oxide red 1.0%, KST-202 defoamer 0.2%, water 23.5%.
[0036] A production process for 3D printing sand mold water-based flow coating, comprising the following steps:
[0037] a. Pretreatment of sodium bentonite and sepiolite powder: Mix 3% bentonite and 1% sepiolite with water at a ratio of 1:1 under stirring, completely disperse evenly, and let stand for 12-24 hours to obtain a pretreatment composite suspension slurry;
[0038] b. Pretreatment of polyvinyl alcohol: weigh 4 times the mass of polyvinyl alcohol in a bucket, slowly add 0.5% polyvinyl alcohol under stirring conditions, and then fully stir until it is completely dissolved, and filter it with a screen (to b...
Embodiment 2
[0043] The production raw materials of a 3D printing sand mold water-based flow coating coating are: zircon powder refractory aggregate 40.0%, andalusite powder refractory aggregate 25.0%, sodium bentonite 2.5%, sepiolite powder 1.0%, polyvinyl alcohol 0.6% , silica sol 0.2%, dioctyl sulfosuccinate sodium salt 0.2%, DY-preservative 0.2%, fluorite 0.7%, iron oxide red 1.4%, KST-202 defoamer 0.2%, water 28%.
[0044] A production process for 3D printing sand mold water-based flow coating, comprising the following steps:
[0045] a. Pretreatment of sodium bentonite and sepiolite powder: Mix 2.5% bentonite and 1% sepiolite with water at a ratio of 1:1 under stirring, completely disperse evenly, and let stand for 12-24 hours to obtain a pretreatment composite suspension slurry;
[0046] b. Pretreatment of polyvinyl alcohol: weigh 4 times the mass of polyvinyl alcohol in a bucket, slowly add 0.6% polyvinyl alcohol under stirring conditions, and then fully stir until it is complete...
Embodiment 3
[0051] The production raw materials of a 3D printing sand mold water-based flow coating coating are: white corundum refractory aggregate 40.0%, high alumina fine powder refractory aggregate 25.0%, sodium bentonite 2.5%, sepiolite powder 1.0%, polyvinyl alcohol 0.6% , phosphate 0.2%, dioctyl sulfosuccinate sodium salt 0.2%, DY-preservative 0.2%, fluorite 0.7%, iron oxide red 1.4%, KST-202 defoamer 0.2%, water 28%.
[0052] A production process for 3D printing sand mold water-based flow coating, comprising the following steps:
[0053] a. Pretreatment of sodium bentonite and sepiolite powder: Mix 2.5% bentonite and 1.0% sepiolite with water at a ratio of 1:1 under stirring, completely disperse evenly, and let stand for 12-24 hours to obtain a pretreatment composite suspension slurry;
[0054] b. Pretreatment of polyvinyl alcohol: weigh 4 times the mass of polyvinyl alcohol in a bucket, slowly add 0.6% polyvinyl alcohol under stirring conditions, and then fully stir until it is...
PUM
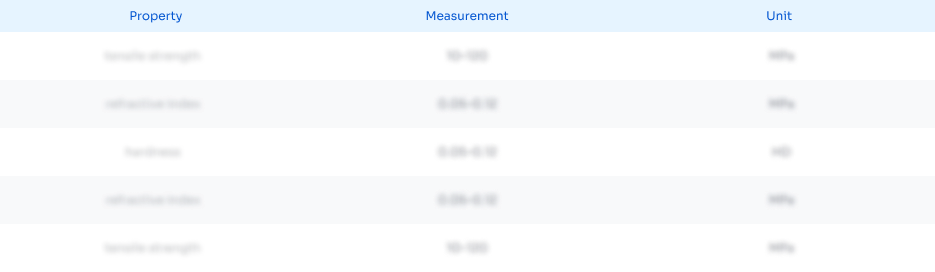
Abstract
Description
Claims
Application Information

- R&D
- Intellectual Property
- Life Sciences
- Materials
- Tech Scout
- Unparalleled Data Quality
- Higher Quality Content
- 60% Fewer Hallucinations
Browse by: Latest US Patents, China's latest patents, Technical Efficacy Thesaurus, Application Domain, Technology Topic, Popular Technical Reports.
© 2025 PatSnap. All rights reserved.Legal|Privacy policy|Modern Slavery Act Transparency Statement|Sitemap|About US| Contact US: help@patsnap.com