A kind of preparation method of resin containing water-soluble plasticizer and polyurethane
A plasticizer, water-soluble technology, applied in the field of leather resin, can solve problems such as environmental pollution and damage to workers' health, and achieve the effect of large molecular weight and non-volatile
- Summary
- Abstract
- Description
- Claims
- Application Information
AI Technical Summary
Problems solved by technology
Method used
Image
Examples
Embodiment 1
[0037] Step 1: Add 1 mol of dimethyl glutarate that has been refined and dehydrated into a closed reaction kettle, and simultaneously add 30% sodium methoxide in anhydrous methanol solution containing 0.05 mol of sodium methoxide, and stir under nitrogen protection. 150rpm, then filled with 1.6mol dimethylamine gas, the reaction temperature is 30°C, the reaction time is 7h, the reaction of transesterification into amide occurs, and N 1 ,N 1 ,N 5 ,N 5 - Tetramethylglutaramide and methyl 5-(dimethylamino)-5-oxopentanoate.
[0038] Step 2: Add 85% phosphoric acid aqueous solution containing 0.15 mol of phosphoric acid to the reaction kettle, stir at 150 rpm, and neutralize for 2 hours to generate dimethylamine phosphate and sodium phosphate to remove sodium ions in step 1 and excess dimethylamine.
[0039] Step 3: Move the mixture treated in Step 2 to a filter kettle, and filter to remove dimethylamine phosphate and sodium phosphate.
[0040] Step 4: methanol and water are r...
Embodiment 2
[0044] Step 1: Add 1 mol of dimethyl glutarate that has been refined and dehydrated into a closed reaction kettle, and simultaneously add 30% sodium methoxide in anhydrous methanol solution containing 0.06 mol of sodium methoxide, and stir under nitrogen protection. 200rpm, then filled with 1.8mol dimethylamine gas, the reaction temperature is 40°C, the reaction time is 6h, the reaction of transesterification into amide occurs, and N 1 ,N 1 ,N 5 ,N 5 - Tetramethylglutaramide and methyl 5-(dimethylamino)-5-oxopentanoate.
[0045] Step 2: Add 85% phosphoric acid aqueous solution containing 0.26 mol of phosphoric acid in the above reaction kettle, stir at 200 rpm, and neutralize for 2 hours to generate dimethylamine phosphate and sodium phosphate to remove sodium ions in step 1 and excess dimethylamine.
[0046] Step 3: Move the mixture treated in Step 2 to a filter kettle, and filter to remove dimethylamine phosphate and sodium phosphate.
[0047] Step 4: methanol and water a...
Embodiment 3
[0051] Step 1: Add 1.0 mol of refined 2-methyl-glutaric acid dimethyl ester into a closed reaction kettle, and simultaneously add 30% sodium methoxide in anhydrous methanol solution containing 0.07 mol of sodium methoxide, under nitrogen protection Stir at a stirring speed of 200rpm, then fill with 2.1 mol of dimethylamine gas, the reaction temperature is 50°C, and the reaction time is 6h. The transesterification reaction to amide occurs to generate 2-methyl-5-dimethylcarbamoylvaleric acid methyl ester, methyl 4-methyl-5-dimethylcarbamoylvalerate and dimethyl 2-methyl-1,5-bis(dimethylamino)glutarate.
[0052] Step 2: Add 85% phosphoric acid aqueous solution containing 0.37 mol of phosphoric acid in the above reaction kettle, the stirring speed is 200rpm, and the neutralization reaction time is 2h to generate dimethylamine phosphate and sodium phosphate to remove the sodium ions in step 1 and excess dimethylamine.
[0053] Step 3: Move the mixture treated in Step 2 to a filter...
PUM
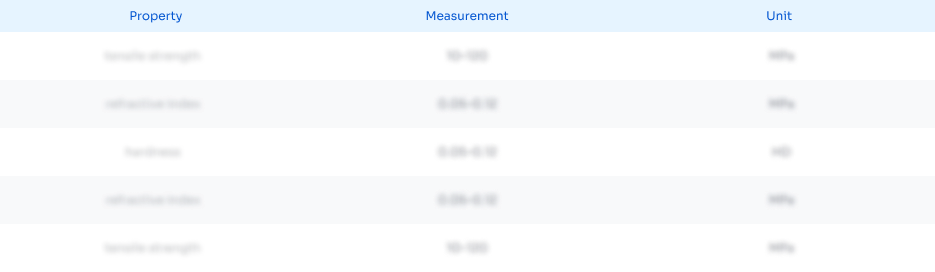
Abstract
Description
Claims
Application Information

- R&D
- Intellectual Property
- Life Sciences
- Materials
- Tech Scout
- Unparalleled Data Quality
- Higher Quality Content
- 60% Fewer Hallucinations
Browse by: Latest US Patents, China's latest patents, Technical Efficacy Thesaurus, Application Domain, Technology Topic, Popular Technical Reports.
© 2025 PatSnap. All rights reserved.Legal|Privacy policy|Modern Slavery Act Transparency Statement|Sitemap|About US| Contact US: help@patsnap.com