A processing method of an automobile one-axis forging die
A processing method and mold technology, applied in the field of mold processing, can solve problems such as short service life, and achieve the effect of eliminating cutting stress, eliminating stress and stable performance.
- Summary
- Abstract
- Description
- Claims
- Application Information
AI Technical Summary
Problems solved by technology
Method used
Examples
Embodiment 1
[0031] A kind of processing method of automobile one-axis forging mold of the present embodiment, its processing steps are:
[0032] Step 1. Raw material preparation, using a round bar blank to prepare for forging. The components of the round bar blank are calculated by weight percentage: C: 0.43%, Si: 1.10%, Mn: 0.42%, S: ≤0.010%, P: ≤ 0.015%, Cr: 5.0%, Ni: 0.08%, Cu: 0.010%, Mo: 1.25%, and the balance is Fe.
[0033] Step 2. Forging the material with three piers and three pulls, the rough forging ratio of the round bar blank to the blank after forging is 3.8;
[0034] The specific forging process is as follows: heating the blank to 1090°C for the first pier thickening and elongation forging, the forging ratio is 1.7, which is the height ratio after one pier thickening and elongation processing; then the blank Heating to 860°C, carry out the second thickening and elongating forging, the forging ratio is 1.6; after the second forging, heat the workpiece to 860°C, and perform ...
Embodiment 2
[0045] A kind of processing method of automobile one-axis forging mold of the present embodiment, its processing steps are:
[0046]Step 1. Raw material preparation, using a round bar blank to prepare for forging. The components of the round bar blank are calculated by weight percentage: C: 0.41%, Si: 1.08%, Mn: 0.42%, S: ≤0.010%, P: ≤ 0.015%, Cr: 5.2%, Ni: 0.08%, Cu: 0.010%, Mo: 1.25%, and the balance is Fe.
[0047] Step 2. Forging the material with three piers and three pulls, the forging ratio of the round bar blank to the forged blank is 4;
[0048] The specific forging process is as follows: heating the blank to 1100°C for the first pier thickening and elongation forging with a forging ratio of 1.8; then heating the blank to 900°C for the second pier thickening and elongation forging, The forging ratio is 1.6; after the second forging, the workpiece is heated to 860°C, and the third forging pier is thickened and elongated, and the forging ratio is 1.4.
[0049] Step 3,...
Embodiment 3
[0059] A kind of processing method of automobile one-axis forging mold of the present embodiment, its processing steps are:
[0060] Step 1. Raw material preparation, using a round bar blank to prepare for forging. The components of the round bar blank are calculated by weight percentage: C: 0.42%, Si: 1.08%, Mn: 0.41%, S: ≤0.010%, P: ≤ 0.015%, Cr: 5.0%, Ni: 0.10%, Cu: 0.009%, Mo: 1.25%, and the balance is Fe.
[0061] Step 2. Forging the material with three piers and three pulls, the forging ratio of the round bar blank to the forged blank is 4;
[0062] The specific forging process is as follows: heating the blank to 1100°C for the first thickening and elongating forging with a forging ratio of 1.8; then heating the blank to 880°C for the second thickening and elongating forging. The forging ratio is 1.6; after the second forging, the workpiece is heated to 880°C, and the third forging pier is thickened and elongated, and the forging ratio is 1.4.
[0063] Step 3, annealin...
PUM
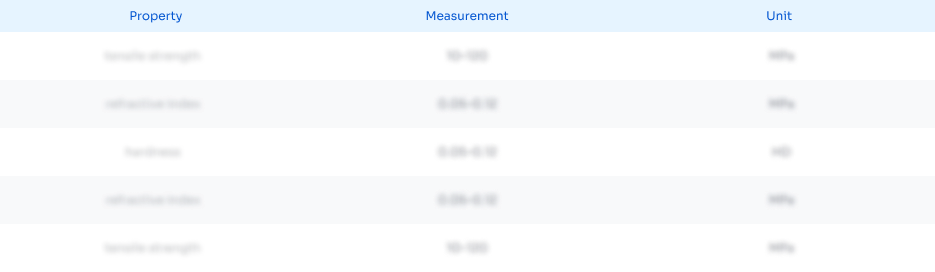
Abstract
Description
Claims
Application Information

- Generate Ideas
- Intellectual Property
- Life Sciences
- Materials
- Tech Scout
- Unparalleled Data Quality
- Higher Quality Content
- 60% Fewer Hallucinations
Browse by: Latest US Patents, China's latest patents, Technical Efficacy Thesaurus, Application Domain, Technology Topic, Popular Technical Reports.
© 2025 PatSnap. All rights reserved.Legal|Privacy policy|Modern Slavery Act Transparency Statement|Sitemap|About US| Contact US: help@patsnap.com