A Fixed Bed Multiphase Atomizing Nozzle
An atomizing nozzle and fixed bed technology, applied in the field of fixed beds, can solve the problems of limited atomization range on the bed surface, uneven liquid phase pipeline size, easy deformation of threads, etc., so as to increase the atomization range and uniformity. The effect of increasing the atomization angle and mixing range, and prolonging the service life
- Summary
- Abstract
- Description
- Claims
- Application Information
AI Technical Summary
Problems solved by technology
Method used
Image
Examples
Embodiment 1
[0070] A fixed bed multiphase atomizing nozzle, such as figure 2 , 8 -shown in 14 and 17, including swirler 1, inner nozzle 2, outer nozzle 4 and installation end seat 9; said installation end seat 9, swirler 1, inner nozzle 2 and outer nozzle 4 are coaxially arranged; all The cyclone 1 is set in the inner nozzle 2 , and the inner nozzle 2 is set in the outer nozzle 4 .
[0071] The head 111 of the swirler 1 is provided with a plurality of first swirl grooves 11;
[0072] The outer wall of the cyclone 1 and the inner wall of the inner nozzle 2 define a liquid phase channel 8;
[0073] The head of the inner nozzle 2 is provided with a liquid phase spray hole 21;
[0074] The liquid phase channel 8 is communicated with the liquid phase nozzle hole 21 through the plurality of first swirl grooves 11;
[0075] The middle part of the head end face of described outer nozzle 4 is provided with the fixing hole 10 that is used to fix described inner nozzle 2 head; The outer wall of...
Embodiment 2
[0090] A fixed bed multiphase atomizing nozzle, such as Figure 3-17 As shown, including the cyclone 1, the inner nozzle 2, the outer nozzle 4, the inner connecting piece 3 and the installation end seat 9; the installation end seat 9, the inner connecting piece, the swirler 1, the inner nozzle 2 and the outer nozzle 4 are arranged coaxially; the swirler 1 is set in the inner nozzle 2, and the inner nozzle 2 is set in the outer nozzle 4.
[0091] The head 111 of the swirler 1 is provided with a plurality of first swirl grooves 11;
[0092] The outer wall of the cyclone 1 and the inner wall of the inner nozzle 2 define a liquid phase channel 8;
[0093] The head of the inner nozzle 2 is provided with a liquid phase spray hole 21;
[0094] The liquid phase channel 8 is communicated with the liquid phase nozzle hole 21 through the plurality of first swirl grooves 11;
[0095] The middle part of the head end face of the outer nozzle 4 is provided with a fixing hole 10 for fixing...
Embodiment approach
[0112] In all the above embodiments, the angle of the swirl hole 41 can be changed through a punching machine according to the needs of the actual atomization process. The implementation method of this kind of swirl hole is briefly described as follows: first determine the oblique tangential angle and hole distance of the holes, and then implement tangential perforation on the outer nozzle along the determined angle and hole distance through piercing machines of different sizes. like Figure 7 As shown in the structural diagram of the outer nozzle, the 5 oblique tangential swirl holes 41 on the outer nozzle have the same angle and direction. If it needs to be changed, it can be realized by the above-mentioned implementation method, which is "variable tangential angle". .
[0113] In all the above embodiments, the cyclone 1 is made of wear-resistant materials.
[0114] The wear-resistant material is preferably nickel-based alloy 718.
[0115] Comparing the atomizing nozzle o...
PUM
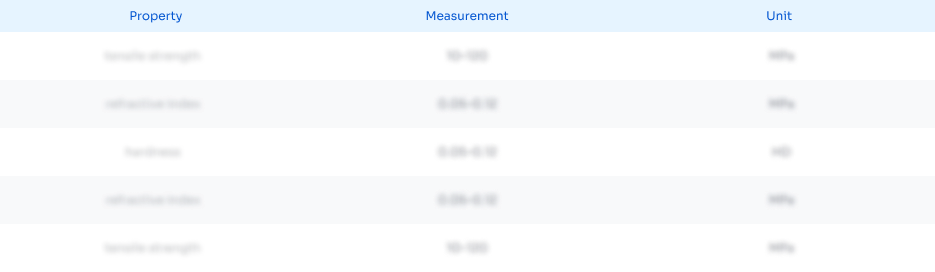
Abstract
Description
Claims
Application Information

- Generate Ideas
- Intellectual Property
- Life Sciences
- Materials
- Tech Scout
- Unparalleled Data Quality
- Higher Quality Content
- 60% Fewer Hallucinations
Browse by: Latest US Patents, China's latest patents, Technical Efficacy Thesaurus, Application Domain, Technology Topic, Popular Technical Reports.
© 2025 PatSnap. All rights reserved.Legal|Privacy policy|Modern Slavery Act Transparency Statement|Sitemap|About US| Contact US: help@patsnap.com