Manufacturing method for cathode guide layer of chip-type conductive polymer tantalum capacitor
A technology for conducting polymer and tantalum capacitors, applied in electrolytic capacitors, capacitors, coatings, etc., can solve the problems of increasing equivalent series resistance, non-densification, and reducing the conductivity of the polymer layer, and achieve the effect of improving continuity
- Summary
- Abstract
- Description
- Claims
- Application Information
AI Technical Summary
Problems solved by technology
Method used
Examples
Embodiment 1
[0036] 1) Press tantalum powder with a specific volume of 50000 μF V / g into a tantalum compact according to a conventional method, and then sinter it into an anode tantalum block according to a conventional method;
[0037] 2) The anode tantalum block is immersed in nitric acid solution to prepare Ta 2 o 5 medium layer;
[0038] 3) Will prepare Ta 2 o 5 The anode tantalum block of the dielectric layer is immersed in the treatment solution with low water content, solvent and silica modification, and taken out at a speed of 1.0mm / min after immersion for 15 minutes; the pretreatment solution is prepared from the following raw materials in weight percentage: Aminosilane coupling agent 1.0%, fumed silica 0.01%, water 5%, methanol 60%, n-butanol 33.99%; place at 25°C for 20min, and dry at 180°C to form a film;
[0039] 4) Synthesize a conductive polymer film on the surface of the pretreated anode tantalum block as a cathode guiding layer according to a conventional method;
[0...
Embodiment 2
[0042] The difference from Example 1 is that the immersion time in step 3) is 10min, and the treatment liquid includes: 0.3% epoxy silane coupling agent, 0.01% fumed silica, 5% water, 60% ethanol, isopropanol 34.69%. Place at 25°C for 20min, and dry at 170°C to form a film.
Embodiment 3
[0044] The difference from Example 1 is that the immersion time in step 3) is 10 minutes, and the treatment liquid includes: 0.6% of aminosilane coupling agent, 0.2% of epoxy silane, 0.02% of fumed silica, 6% of water, 56% of methanol %, propanol 37.18%. Place at 25°C for 20min, and dry at 190°C to form a film.
PUM
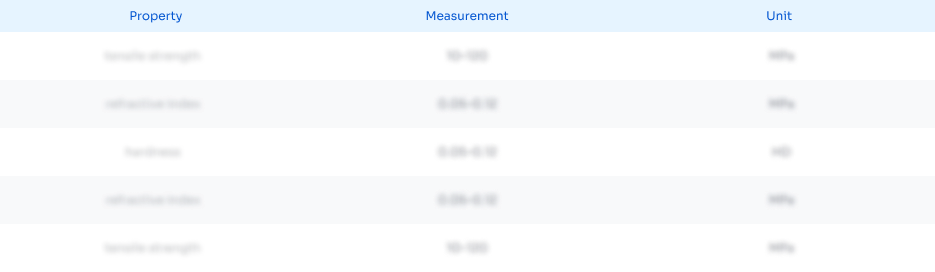
Abstract
Description
Claims
Application Information

- R&D Engineer
- R&D Manager
- IP Professional
- Industry Leading Data Capabilities
- Powerful AI technology
- Patent DNA Extraction
Browse by: Latest US Patents, China's latest patents, Technical Efficacy Thesaurus, Application Domain, Technology Topic, Popular Technical Reports.
© 2024 PatSnap. All rights reserved.Legal|Privacy policy|Modern Slavery Act Transparency Statement|Sitemap|About US| Contact US: help@patsnap.com